Spis treści
Lean Management – definiowanie pojęcia
LEAN to nie jest akronim, bądź jakikolwiek skrót. Tłumaczenie na język polski jako chudy czy szczupły nie w pełni odzwierciedla istotę tego słowa. Pojęcie Lean w kontekście zarządzania w wąskim znaczeniu tłumaczone jest jako wyszczuplanie, odchudzanie, efektywność bez marnotrawstwa[1], szerzej rozumiane jest jako elastyczność (umiejętność szybkiego dostosowywania się do zmian), sprężystość (szybkość i dynamika reakcji na zmiany)[2] oraz zwinność (agile – oznacza zdolność do przetrwania i rozwijania się w warunkach nie dających się przewidzieć)[3]. W zarządzaniu pojęcie Lean definiowane jest w różnych kontekstach. Lean może być rozumiany jako[4]:
- określone działanie np. lean’owanie procesów, odchudzanie organizacji, doskonalenie;
- zestaw cech przypisanych procesowi, jednostce organizacyjnej, organizacji np. szczupłość, zwinność, szybkość, adaptacyjność, doskonałość np. szczupła organizacja, odchudzone procesy;
- nazwa własna określająca zadania jednostki, zespołu, specjalistów np. drużyna Lean menedżer Lean, konsultant Lean itp.
Nazwa Lean Management pojawiła się po raz pierwszy w publikacji J.F. Krafcika pt. Triumph of the lean production system w 1988 r.[5]. Natomiast istotę koncepcji przedstawili w 1990 r. J.P.Womack’a, D.T. Jones’a i D. Ross’a w przełomowej dla zrozumienia idei lean thinking książki: The machine that Changed the World (Maszyna, która zmieniła świat)[6]. W publikacji opisali oni kompleksowo rozwiązania stosowane w zakładach produkcyjnych Toyoty w ramach koncepcji Toyota Production System TPS.
Pomimo długiej historii rozwoju tej koncepcji, nadal trudno w literaturze przedmiotu i praktyce działania odnaleźć jedną definicję Lean Management. Początkowo Lean Management traktowana była jako koncepcja osiągania doskonałości operacyjnej, z czasem ewoluowała w holistyczną filozofię myślenia o zarządzaniu organizacją. House of Lean opisujący TPS, skupia się głównie na narzędziach (Hoshin Kanrii, Jidoka, Just-in-Time, 5S, zarządzanie wizualne, 7 narzędzi jakości, standardowe procedury operacyjne, Gemba)[7]. Rozwój koncepcji TPS zaowocował stworzeniem szerszego podejścia w postaci Lean Enterprise House. U podstawy leży wyzwanie nieustającej adaptacji do potrzeb klientów, pracowników oraz środowiska. Podkreśla się konieczność głębszego angażowania ludzi w proces zmian poprzez Kaizen, prace zespołową, Gemba. Filarami tego podejścia są nieustanne doskonalenie oraz szacunek dla ludzi. Toyota Production System w oparciu o zasady Toyota Way ewoluuje w Thinking People System[8]. Określa się go jako prawdziwą duszę Lean. Podejście to opiera się na nieustannym uczeniu i eksperymentowaniu w procesie nieustannego doskonalenia. Gdyż stare, tradycyjne myślenie i podejście do rozwiązywania problemów daje te same przewidywalne wyniki.
Filozofia Lean Thinking koncentruje się przede wszystkim na oszczędnym działaniu, tzn. podnoszeniu sprawności działania poprzez eliminację marnotrawstwa, zminimalizowanie marnotrawstwa oraz kontrolowanie przepływu wartości dodanej[9]. Womack i Jones[10] definiują Lean Thinking jako
niekończące się przekształcanie marnotrawstwa w wartość z perspektywy klienta.
Przeprowadzona analiza literatury pokazuje, że Lean Management jest definiowany wielowymiarowo jako[11]: system zarządzania, strategia doskonalenia, podejście do zmiany organizacyjnej, kultura organizacyjna, zbiór metod i narzędzi doskonalenia. Lean Management rozumiany jest jednocześnie w wymiarze strategicznym, jako filozofia myślenia o zarządzaniu organizacją oraz metodyka i praktyka działania, która dostarcza technik i narzędzi pozwalających na poprawę jakości oraz redukcję marnotrawstwa w sferze operacyjnej działania organizacji. Współcześnie obejmuje wymiar projektowania organizacji i procesów (odkrywanie, definiowanie, projektowanie) oraz wykonania (rozwijanie, dostarczanie)[12]. Należy podkreślić, że Lean nie służy do osiągania szybkich efektów ekonomicznych i drapieżnej optymalizacji kosztów. Źle wdrażana i rozumiana koncepcja Lean doprowadziła do jeszcze innego tłumaczenia pojęcia LEAN Less Employees Are Needed[13].
Lean Management – inspiracje i etapy rozwoju
Lean Management czerpie z wielu koncepcji zarządzania, które były tworzone w różnych uwarunkowaniach politycznych, gospodarczych, społecznych i kulturowych. W historii Lean Management wzajemnie nieustannie przenikały nurt amerykański oraz japoński. Nośnikiem inspiracji, innowacji i wiedzy byli wybitni naukowcy, przedsiębiorcy, menedżerowie i eksperci, a wypracowane przez nich zasady, metody i narzędzia stały swoistą skrzynką narzędziową – Lean Toolbox . Na rys. 1 schematycznie ujęto rozwój koncepcji Lean Management na przestrzeni XIX, XX i XXI w.
Należy pamiętać, że pomimo, że nazwa Lean pojawiła się po raz pierwszy w publikacji John’a Krafcika w 1988 r.[14], jako źródło tej koncepcji wskazuje się czas rewolucji przemysłowej.
Podniesienie wydajności i jakości produkcji masowej stało się możliwe dzięki wprowadzeniu nowych rozwiązań w postaci części zamiennych oraz linii montażowej (Eli Whitney (1765 – 1825)[15], co pozwoliło na standaryzację wyrobów oraz procesów. Rozwiązania te zostały wykorzystane m.in. przez Henry’ego Forda (1863 – 1947). Jako pierwszy stworzył on kompleksową strategię produkcji, która obejmowała wszystkie aspekty procesu produkcyjnego takie jak: ludzie, maszyny i produkty i ich systemowe powiązania. Efektem tego było stworzenie całościowej koncepcji linii produkcyjnej opartej na masowym przepływie produktów na ruchomej linii montażowej.[16]. W Lean Management wykorzystujemy również wyniki prac prekursorów naukowego zarządzania, szczególnie w zakresie studiów nad procesami pracy robotników. Frederick Winslow Taylor (1856-1915) pod koniec XiX w. badał i mierzył czas każdego działania robotnika oraz projektował bardziej efektywne sposoby wykonywania pracy. Wyniki swoich badań sfomułował w postaci zasad naukowego zarządzania[17]. Podobne badania prowadziło małżeństwo Frank (1868 – 1924) i Lilian Gilbreth (1878-1972). Zajmowali się oni badaniem procesów pracy oraz psychologicznymi aspektami pracy robotników. Na podstawie analizy procesów pracy tworzyli standardy dotyczące materiałów oraz techniki pracy. Lilian Gilbrecht badała m.in. wpływ motywacji na efekty pracy. Podkreślali konieczność szkolenia robotników. Zwraca się uwagę, że prace, które powstały w nurcie klasycznego zarządzania na przełomie XIX i XX w. były mocno ukierunkowane na eliminację marnotrawstwa poprzez szukanie jego przyczyn z wykorzystaniem metod analizy procesów pracy. Początkowo badania skupiały się na eliminacji marnotrawstwa materialnego (materiały, maszyny, czas, braki itp.), później marnotrawstwa niematerialnego (brak szkoleń, nieodpowiednia motywacja, niewłaściwa organizacja stanowisk pracy i pracy itp.)[18].
Na koniec XIX w. datuje się pierwsze rozwiązania, które stały się podstawą do stworzenia Systemu Produkcyjnego Toyoty (Toyota Production System TPS). Młody japoński wynalazca i przedsiębiorca Sakichii Toyoda (1861-1930) pracując nad udoskonaleniem krosna tkackiego stworzył szereg zasad, które stały się fundamentami TPS. Należą do nich m.in.: genchi genbutsu (zarządzanie przez fakty, aktywne angażowanie ludzi), jidoka (automatyzacja z ludzką twarzą, krosno zatrzymywało się automatycznie w przypadku zerwania się lub braku nici). Jedną z ważnych inspiracji w jego pracy była książka Samuela Smilesa zatytułowana Self-Help (pol. Pomoc własna)[19]. Autor podkreślał w niej rolę ciężkiej pracy, wytrwałości i dyscypliny w doskonaleniu i osiąganiu celów oraz konieczność pracy dla społeczeństwa. Prace kontynuował Kichiro Toyoda (1894-1952), który w latach 30’ XX założył Toyota Motor Company. Jako jego oryginalny wkład w rozwój TPS uznaje się koncepcję dostawy na czas. Została ona zainspirowana jego podróżą badawczą zakładów Forda w Michigan, przy okazji zebrał ciekawe spostrzeżenia na temat działania supermarketów (towar na półkach był uzupełniany w chwili, kiedy go zabrakło).
Lata 30’ XX wieku to czas rozwoju metod statystycznej kontroli procesów (ang. Statistical Process Control). Celem jest nadzorowanie zdolności stabilności jakościowej procesów produkcyjnych w celu zapobiegania niezgodności oraz doskonalenia produktów[20]. Jako prekursora SPC uważa się Walter Andrew Shewhart’a (1891 – 1967). Opracował on kartę kontrolną, która jest wykorzystywana w Six Sigma oraz cykl Shewarta, rozwinięty i spopularyzowany w latach późniejszych przez Willima Edwards’a Deminga (1900-1993) w postaci cyklu PDCA.
Do rozwoju Lean Management przyczyniły się prace twórców Kompleksowego Zarządzania Jakością takich jak Willima Edwards Deming, Joseph Moses Juran, Philip Bernard Crosby oraz Armand Vallim Feigenbaum[21]. Szczególnie koncepcje Edwardsa Deminga, który po II wojnie światowej został wysłany przez rząd USA do Japonii, znacząco wpłynęły na kształt TPS[22]. Należały do nich między innymi poszerzenie definicji klienta o klienta wewnętrznego, wprowadzenie cyklu nieustannego doskonalenia i uczenia się PDCA (nazywany często cyklem Deminga) oraz SPC. Inspiracja Deminga była też twórczo rozwijana przez japońskich naukowców i inżynierów takich jak: Masaaki Imai (Kaizen – metoda ciągłych usprawnień)[23], Genichi Taguchi (funkcja strat jakości, sterowanie jakością, projektowanie eksperymentów), Kaoru Ishikawa (koła jakości, 7 narzędzi jakości)[24], Yoji Akao (Quality Function Deployment QFD, Hoshin Kanrii)[25], Taiichi Ohno (kanban, just in time JIT, klasyfikacja marnotrawstwa muda, technika 5Whys, Krąg Ohno – bezpośrednia obserwacja, gemba)[26].
Kamieniem milowym w rozwoju koncepcji Lean Management było z pewnością stworzenie Toyota Production System TPS[27]. Jego twórcy oparli go na własnych rozwiązaniach (m.in. jidoka, genchi genbutsu, dostawa na czas) oraz doświadczeniach amerykańskich przedsiębiorstw tj. Ford, General Motors (m.in. linia produkcyjna, koncepcja supermarketów, PDCA, SPC, TQM). Na ostateczny kształt TPS wpłynęły również specyficzne uwarunkowania kultury narodowej Japończyków, brak zasobów naturalnych, niska kultura techniczna, gospodarka osłabiona po II wojnie światowej, kontrybucje wojenne oraz brak kapitału. Do 1965 r. TPS nie był formalnie udokumentowany, dlatego przez wiele lat nie był zauważany w teorii i praktyce zarządzania[28].
Pierwszy kryzys paliwowy lat 80’ XX w. oraz wzrastająca konkurencyjność wyrobów japońskich doprowadziły do wzrostu zainteresowania japońskimi metodami zarządzania produkcją. Zainaugurowany przez Massachusetts Institute of Technology program pod nazwą Motor Vehicle Program zaowocował opracowaniem w 1984 r. książki The Future of the Automobile[29]. Wyniki badań stały się podstawa do napisania w 1990 r. przez J.P.Womack’a, D.T. Jones’a i D. Ross’a przełomowej dla zrozumienia idei lean thinking książki: The machine that Changed the World (Maszyna, która zmieniła świat)[30].
Początkowo koncepcja Lean była wdrażana w przedsiębiorstwach produkcyjnych przyjmując nazwę Lean Production, czy Lean Manufacturing. Jak podkreśla Liker, koncepcja ta była niezrozumiała dla amerykańskich przedsiębiorców, gdyż produkcja po II wojnie światowej koncentrowali się oni się paradygmacie opartym na obniżaniu kosztów dzięki wykorzystaniu efektu ekonomii skali[31]. Lata 80’ XX wieku przyniosły popularyzację paradygmatu opartego na jakości. Prace prekursorów zarządzania jakością pokazały, że skupienie się na jakości prowadzi do większego obniżenia kosztów niż ich tradycyjna kontrola. Lata 90’ XX w. to wzrastająca popularność idei Lean thinking. Nowy paradygmat działania opiera się na dostarczaniu wartości klientowi poprzez eliminację marnotrawstwa w procesie nieustannego doskonalenia z zachowaniem szacunku dla ludzi. Stało się to dużym wyzwaniem i jednocześnie nowym impulsem do doskonalenia zarządzania nie tylko w sektorze produkcji. Koncepcja Lean Management zaczęła być z powodzeniem wykorzystywana w sektorze usług (Lean Services), sektorze publicznym (Lean Government), edukacji (Lean Education, Lean Higher Educatioh), ochrony zdrowia (Lean Healthcare), budownictwie (Lean Construction), Lean NGO (non governmental organisations), Lean Consumption i wielu innych. Gromadzone doświadczenia pokazują, że jest to koncepcja uniwersalna, która może być wykorzystana do doskonalenia zarządzania w każdych uwarunkowaniach kulturowych, technicznych, politycznych, społecznych, ekonomicznych i organizacyjnych. Lean Management jest cały czas rozwijany łącząc w sobie lub łącząc się z innymi metodami i narzędziami doskonalenia takimi jak: zarządzania procesami, zarządzanie jakością (w tym normy ISO), Six Sigma.
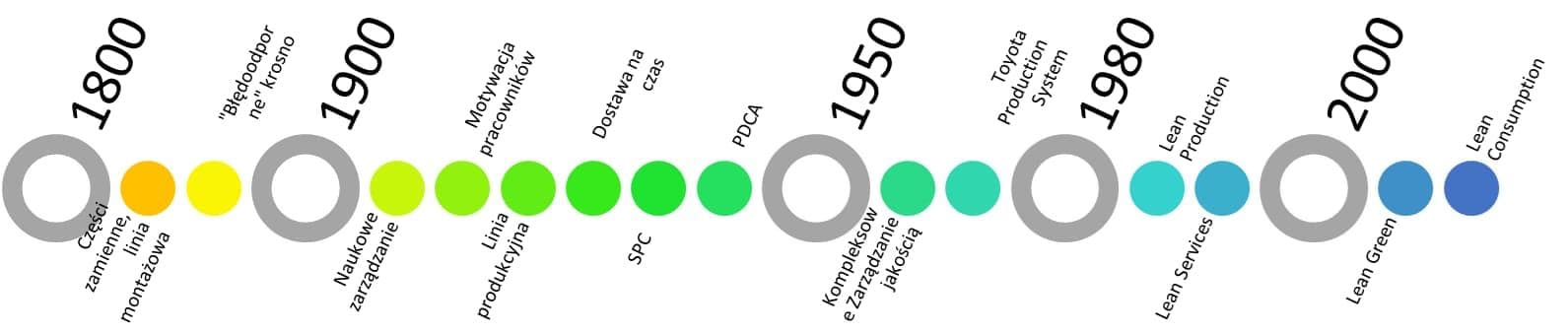
Fundamentalne założenia koncepcji Lean
Zasady Lean według Likera
W literaturze przedmiotu można napotkać na liczne próby usystematyzowania fundamentalnych założeń koncepcji Lean Management. Jako pierwsi dokonali tego Womack’a, Ross’a i Jones’a w książce The machine that Changed the World. Pięć fundamentalnych zasad Lean wg Autorów to:
- Dokładne ustalenie wartości dla konkretnego produktu, usługi (value).
- Identyfikacja strumienia wartości dla każdego produktu (value stream)
- Zapewnienie niezakłóconego przepływu (flow)
- Tworzenie wartości wtedy gdy jest ona oczekiwana przez klienta (pull)
- Dążenie do doskonałości (continuous improvement)
Zasady Lean według Womack’a, Ross’a i Jones’a
J.K. Liker w książce the Toyota Way rozwinął te zasady tworząc 14 wytycznych uporządkowanych w czterech obszarach[32]:
- Rozwiązywanie problemów – ciągła poprawa i uczenie się:
- Angażowanie się osobiście, aby gruntowanie zrozumieć sytuację,
- Podejmować decyzje powoli, w drodze konsensusu i starannie rozważać możliwości
- Szybko wdrażać decyzje
- Zostać organizacją uczącą się dzięki niestrudzonej ocenie tego co robimy i ciągłej poprawie
- Ludzie i partnerzy – szacunek, rzucanie wyzwań – wychowanie
- Wychować liderów, którzy gruntownie rozumieją pracę, żyją ogólną koncepcją firmy i nauczają innych
- Wykształcić wyjątkowych ludzi i zespoły realizujące ogólną koncepcję firmy
- Szanować szeroką sieć partnerów i dostawców, rzucając im wyzwania i pomagając im w doskonaleniu
- Proces – Eliminacja marnotrawstwa
- Stworzyć ciągły i płynny proces ujawniania problemów
- Wykorzystać systemy ciągnięcia, aby uniknąć nadprodukcji
- Wyrównać obciążenie pracą
- Przerywać pracę gdy pojawia się problem
- Standardowe zadania i procesy są podstawą ciągłej poprawy i upełnomocnienia pracowników
- Stosować technologię służącą pracownikom i procesom
- Stosować kontrolę wizualną, by żaden problem nie pozostał w ukryciu
- Ogólna koncepcja – Dalekosiężne myślenie
- Opierać decyzje w zarządzaniu na dalekosiężnej koncepcji – nawet kosztem krótkoterminowych wyników finansowych
W 2001 r. prezes Toyoty Fujio Cho zmodyfikował zasady Toyoty wprowadzając nowe wytyczne pod nazwa Toyota Way. Jako najważniejsze z nich określił[33]:
- Wyzwanie – określenie długoterminowej wizji i dążenie to sprostania wyzwaniom z odwagą oraz kreatywnością, której wymaga realizacja wizji.
- Kaizen – dążenie do nieustannego doskonalenia. Żaden proces nie może być traktowany jako perfekcyjny, zawsze jest przestrzeń dla usprawnień.
- Genchi Genbutsu – pójście do źródła problemów po to, aby zebrać fakty i dane, w celu podjęcia właściwych decyzji, zbudowania konsensusu i osiągnięcia celów.
- Szacunek – podejmowanie wszelkich wysiłków, aby zrozumieć innych, akceptacja odpowiedzialności i budowanie zaufania.
- Praca zespołowa - tworzenie i zwiększanie możliwości rozwoju indywidualnego oraz poprzez działanie zespołów.
Fundamentem zmiany wytyczonej zasadami Lean Management jest zrozumienie istoty tej koncepcji definiowane poprzez pojęcia takie jak:
Szacunek dla ludzi
Teoretycy i praktycy przestrzegają, że brak okazywania szacunku ludziom prowadzi do upadku większości programów Lean. Szacunek dla ludzi jest definiowany i rozumiany poprzez wartości takie jak zaufanie, prawo do kwestionowania utartych schematów działania, dobrowolność, bezpieczeństwo, zobowiązanie, odpowiedzialność, współpraca, uczciwość, słuchanie, zrozumienie i empatia. Wartości te są podstawą do budowania relacji pomiędzy pracownikami oraz przełożonymi w organizacji, a także budują zaangażowanie pracowników w program zmiany.
Nieustanne doskonalenie
Drugą osią, wokół której jest budowana Kultura Lean to doskonalenie. Doskonalenie rozumiane jest wielowymiarowo jako ciągłe uprawnianie oraz trwała kultura codziennej pracy. Wartość jaką jest doskonalenie opiera się na otwartości na zmiany, elastyczności, proaktywności, zdrowym rozsądku, elastyczności, podejmowaniu decyzji na podstawie faktów, eliminowaniu marnotrawstwa i tworzeniu wartości, mądrości oraz trwałości i ciągłości zmian. Uniwersalnym modelem doskonalenia jest cykl PDCA (Plan Do Check Act – zaplanuj, zrealizuj, sprawdź i doskonal).
Wartość/wartość dodana
Marnotrawstwo
Marnotrawstwo w koncepcji Lean to każde działanie, które zużywa zasoby, a nie dodaje wartości dla klienta[35]. Źródłem marnotrawstwa są dwie kategorie działań:
- działania nietworzące wartości, ale niezbędne do prawidłowej realizacji usługi BVA/NNVA (Business Value Added/Necessary Non Value Added) (np. wynikające z przepisów prawa oraz regulaminów wewnętrznych, zwyczajów i tradycji szkoły, technologii realizacji procesów np. systemów wspomagania zarządzania itp.)
- oraz działania nietworzące wartości, zbędne z punktu widzenia klientów zewnętrznych oraz wewnętrznych organizacji (NVA Non Value Added).
Japończycy definiowali trzy podstawowe kategorie marnotrawstwa (MUDA):
- Muda (marnotrastwo) jest to jakakolwiek forma marnotrawstwa w procesie.
- Mura (nieregularność) nierównomierne rozłożenie pracy maszyn lub ludzi.
- Muri (nadmierne obciążenie) to nieracjonalne przeciążenie maszyn lub ludzi.
Klasyczny podział źródeł marnotrawstwa, zaproponowany przez T. Ohno 7 Wastes, obejmuje następujące kategorie[36]:
- Over-production – nadprodukcja (np. zbyt duża ilość produktów w stosunku do zapotrzebowania klienta).
- Waiting – czekanie (np. oczekiwanie na dokumenty, wsparcie techniczne, oczekiwanie na zgody, akceptacje, podpisy, pracę innego pracownika, półprodukty).
- Unnecessary transport – zbędny transport/przemieszczanie (np. dokumentów, produktów, surowców).
- Over – processing – nadmierne lub niewłaściwe przetwarzanie (np. zbyt wiele czynności i działań, zbyt wiele informacji, procedur, podpisów, osób zaangażowanych w proces, spotkań).
- Incorect inventory – nadmierny stan zapasów (np. zbędne zapasy międzyoperacyjne, surowców, półproduktów, pracy w toku, produktów).
- Unnecessary movement – zbędne ruchy (np. zbędne przemieszcaanie pomiędzy maszynami, stanowiskami pracy, zbędne czynności np. uporządkowanie stanowiska pracy po poprzednim pracowniku).
- Defects – defekty (np. błędy, niezgodności, pomyłki, wadliwe produkty, usługi).
Dodatkowo dodaje się jeszcze 8 kategorię – niewykorzystana kreatywność pracowników[37] (np. prowadzenie przez pracowników zajęć dydaktycznych i badań, w których nie są specjalistami, mało precyzyjne zakresy czynności, które powodują angażowanie pracowników w działania niezgodne z ich kluczowymi kompetencjami).
Często stosuje się też skrót TIMWOODS dla określenia powyższych kategorii (transport, inventory, motion, waiting, overburden, over-processing, defects, skills).
Analiza literatury przedmiotu, wskazuje, że systematyka źródeł marnotrawstwa nie może być bezrefleksyjnie adaptowana z przedsiębiorstw produkcyjnych do sektora usług publicznych. Na podstawie badań prowadzonych w brytyjskich organizacjach publicznych zaproponowano pewną modyfikację kategorii marnotrawstwa, zalicza się tutaj[38]:
- opóźnienia (delay)
- duplikowanie się (duplication)
- niepotrzebny ruch (unnecesary movement)
- niejasna komunikacja (unclear communication)
- nieprawidłowe zapasy (incorect inventory)
- utracone szanse (opportunity lost)
- błędy (errors)
- ludzie (people)
Zgodnie z zasadą Pareto, ponad 80% marnotrawstwa w zarządzaniu organizacją ma charakter systemowy, i jest niezależne od działania pojedynczych pracowników. Źródłem marnotrawstwa są błędne, nieefektywne i nieskuteczne rozwiązania wbudowane w sytemu zarządzania oraz brak umiejętności zarządzania ludźmi. Za taki stan rzeczy odpowiadają menedżerowie, zgodnie z tezą Edwardsa Deminga, który twierdził, że za 80% problemów w organizacji odpowiadają zarządzający.
Usprawnianie procesów polega na identyfikowaniu marnotrawstwa (audyt marnotrawstwa, mapowanie strumienia wartości), określaniu jego kategorii (muda, 7 wastes lub TIMWOODS) i rodzaju (działania BVA/NNVA lub NVA) oraz zaprojektowaniu działań mających na celu jego eliminacje w kolejnych cyklu działania.
Lean w procesie tworzenia kultury organizacyjnej ukierunkowanej na nieustanne doskonalenie
Lean Management jest definiowany jako zmiana kulturowa, przy czym dojrzałość Kultury Lean jest jednocześnie czynnikiem, który wpływa na implementację koncepcji Lean Management, jak również jej efektem[39]. Istnieje zgodność autorów, że kultura organizacyjna jest istotnym czynnikiem sukcesu Lean Management w organizacjach[40]. Badacze i praktycy coraz bardziej doceniają jej znaczenie, dostrzegając, że zmiany techniczno-organizacyjne są zdecydowanie prostsze do przeprowadzenia[41], ale ich sukces i trwałość są uzależnione od zbudowania właściwej kultury organizacyjnej. Zdaniem Likera szczupłe myślenie wymaga głębokiej transformacji kulturowej[42]. Zatem warunkiem niezbędnym sukcesu jest stworzenie kultury organizacyjnej, która będzie wpierała wysiłki w zakresie nieustannego doskonalenia.
Można spotkać różne jej nazwy: Lean Culture Change[43], kultura szczupłej organizacji[44], culture of continuous improvement and change[45], Culture of Performance Improvement[46].
Można zatem postawić pytanie czym jest kultura Lean. Opierając się na koncepcji Sheina (2004) można kulturę Lean zdefiniować jako: Kultura Lean to zharmonizowany, zwarty i spójny wzorzec zachowań będący wynikiem wspólnego uczenia się w procesie doskonalenia organizacji w oparciu o fundamentalne założenia, system i metody Lean Management[47]. W takim ujęciu zakłada się, że kultura organizacyjna jest przedmiotem zarządzania i można ją zmieniać stosując odpowiednie metody i narzędzia Lean Management. Jest to podejście pozytywistyczne. Należy jednak mieć na uwadze, że kultura organizacyjna może też być rozumiana jako zjawisko niejednoznaczne, efemeryczne, trudne do opisania i zarządzania. Zatem często zamiast pojęcia zarządzanie kulturą organizacyjną używa się pojęcia kształtowanie kultury organizacyjnej. Nieprzewidywalność zmiany jaka zachodzi w ludziach oraz ich wzajemnych relacjach uzasadnia takie podejście.
Można wskazać trzy integralne elementy, które stanowią o istocie zmiany ukierunkowanej na kulturę nieustannego doskonalenia. Są to[48]:
- fundamentalne założenia działania organizacji oparte na filozofii Lean Thinking, wartościach Lean, programie/strategii Lean i zasadach Lean),
- system Lean Management obejmuje strukturę organizacyjną, procesy, procedury, zasoby, które wspierają wdrażania Lean Management,
- metody i narzędzia Lean, która mają się one docelowo stać narzędziami codziennej pracy każdego pracownika.
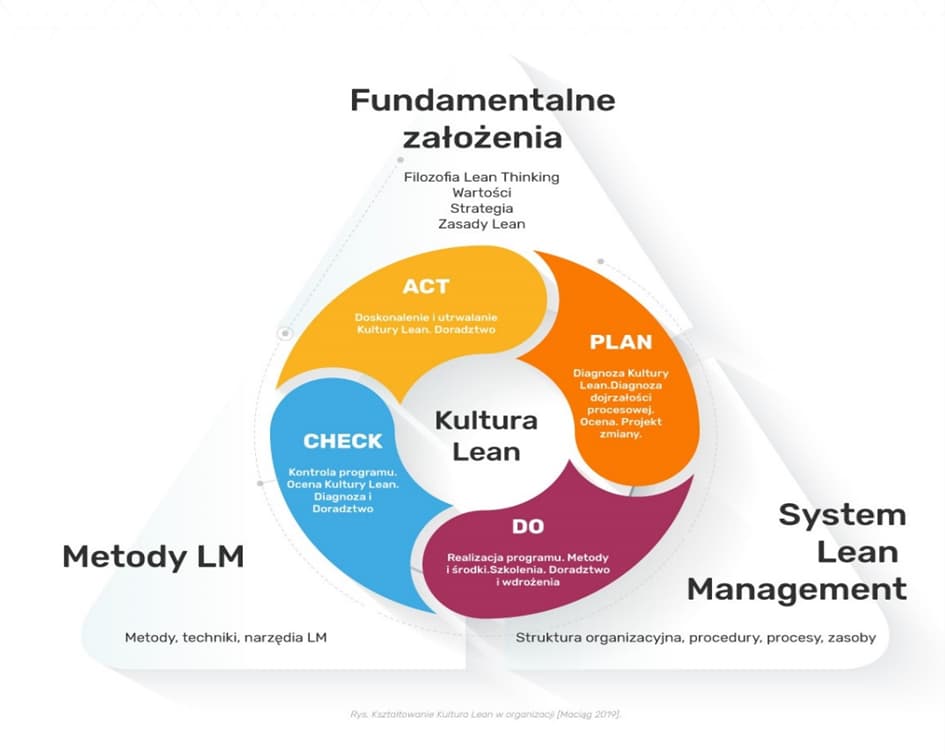
Podstawą do wdrożenia koncepcji Lean management jest głębokie zrozumienie jej istoty. Ważnymi czynnikami jest przekonanie kierownictwa organizacji, że jest to właściwa ścieżka zmiany organizacyjnej oraz głębokie zaangażowanie w ten proces. Istotne znaczenie ma też nieustanne angażowanie pracowników w proces zmiany z okazywaniem im szacunku dla ich pracy i specjalistycznej wiedzy. Lean skupia się na stosunku pracownika do pracy, jak ją rozumie, jaki ma ona dla niego sens, jakie ma związku z nią uczucia, jak sobie radzi z problemami, jak układ się współpraca[49].
Kolejnym istotnym czynnikiem jest stworzenie systemu wsparcia w organizacji. Lean Management System LMS docelowo jest narzędziem realizacji programu zmiany kultury organizacyjnej. Najczęściej tworzą go elementy, takie jak:
- Struktura organizacyjna.
- Procedury (określenie osób odpowiedzialnych za wdrażanie koncepcji, wybór odpowiednich technik i narzędzi oraz określenia wskaźników skuteczności i efektywności, metod monitorowania oraz doskonalenia).
- Zasoby (ludzkie, rzeczowe, finansowane, informacyjne, czas).
Kolejnym integralnym elementem zmiany jest nieustanne doskonalenie kompetencji w zakresie Lean i innych metod i narzędzi nieustannego doskonalenia przez pracowników i menedżerów w organizacji.
Wszystkie wymienione elementy są niezbędne, oddziałują wzajemnie na siebie i warunkują skuteczną zmianę kultury organizacji w kierunku nieustannego doskonalenia. Zatem nie można pominąć żadnego z tych elementów w procesie projektowania i wdrażania zmiany.
Podejścia do wdrażania Lean w organizacji (struktury organizacyjne, procedury, metody i narzędzia)
Jak już wcześniej podkreślono, wdrażanie Lean wymaga stworzenia w organizacji skutecznego systemu wsparcia pracowników, menedżerów i liderów zmian. Organizacje wypracowują równe rozwiązania w tym zakres mając na uwadze swoją kulturę organizacyjną, wielkość, złożoność, posiadane zasoby materialne (przestrzeń, sale, wyposażenie, środki finansowe itp.) oraz ilość doświadczonych specjalistów (Lean facylitatorów, Lean liderów itp.). Poniżej przedstawiony został przegląd najważniejszych stosowanych rozwiązań.
Rozwiązanie organizacyjne | Istota i charakterystyka | Zalety, szanse | Wady, zagrożenia, ryzyka |
Dedykowany odrębny department/zespół (Continuous Improvement CI, Business Improvement lub inny) | W strukturze organizacyjnej tworzony jest odrębny departament, który realizuje zadania związane są z planowaniem zmian, zarzadzaniem zmianą, doradztwem, wsparciem, szkoleniami, doraźną pomocą, monitorowaniem i kontrolą. Zakres działań może być różny. | Przyporządkowanie zadań, odpowiedzialności i uprawnień w zakresie Lean do konkretnej komórki w strukturze szkoły. Czytelność i rozliczalność działań. Wysoka profesjonalizacja. Zmniejszenie kosztów szkoleń zewnętrznych. Łatwiejsze planowanie, powiązanie ze strategią działania i kaskadowanie celów na działalność operacyjną. Łatwiejsza kontrola zasobów i środków przeznaczonych na usprawnienia. Możliwość połączenia z innymi istniejącymi w strukturze jednostkami np. działem ds. jakości i in. | Ryzyko braku niezakłóconego transferu wiedzy i umiejętności do pracowników w organizacji. Odpowiedzialnym za powodzenie wprowadzanych zmian są pracownicy działu, odpowiedzialność jest zdejmowana z barków pracowników i kierownictwa uczelni. Zagrożenie brakiem trwałych zmian w kulturze organizacyjnej, działania uprawiające są dalej traktowane jako epizodyczne eventy a nie stały element, część codziennej pracy pracowników |
Dedykowany pracownik (stanowisko pracy ds. Lean) odpowiedzialny za wdrażanie koncepcji Lean plus formalny zespół/zespoły pracowników (Lean Team). | Tworzone jest stanowisko pracy specjalisty w zakresie Lean, który jest odpowiedzialny za planowanie, wdrażanie, monitorowanie i kontrolę oraz doskonalenie prowadzonych działań. Wsparcie stanowi powołany formalnie zespół tworzony przez pracowników pochodzących z różnych obszarów organizacjii, którzy najczęściej łączą pracę w zespole z codziennymi obowiązkami. | j.w. Swobodny transfer wiedzy pomiędzy ekspertami Lean a innymi pracownikami organizacji. Doskonała znajomość przez ekspertów Lean specyfiki pracy w różnych działach. Zwiększanie poczucia odpowiedzialności wśród pracowników. | Problemy z łączeniem obowiązków zawodowych i pracy w zespole Lean (brak czasu, stres, przeciążenie pracą). Przypisywanie odpowiedzialności za wdrażanie Lean tylko jednej osobie i zespołowi. Zagrożenie brakiem trwałych zmian w kulturze organizacyjnej |
Dedykowany pracownik/specjalista odpowiedzialny za wdrażanie koncepcji Lean plus wewnętrzna sieć specjalistów Lean oraz pracowników zainteresowanych CI | W organizacji tworzona jest wewnętrzna sieć, która łączy pracowników zajmujących się Lean i stosujących tą koncepcje w codziennej pracy (Continous Improvement Partners Program). Celem działania sieci jest wsparcie, wspólne poszukiwanie metod i technik rozwiązywania problemów, wymiana doświadczeń. Sieć posiada wyraźnego wskazanego przez kierownictwo lidera. | Intensywne masowe programy specjalistycznych szkoleń w zakresie Lean i innych metodyk. Swobodny transfer wiedzy pomiędzy ekspertami Lean a innymi pracownikami organizacji. Doskonała znajomość przez ekspertów Lean specyfiki pracy w różnych działach. Zwiększanie poczucia odpowiedzialności wśród pracowników uczelni. Szeroka znajomość metodyki i umiejętność wykorzystania jej w codziennej pracy. Brak barier związanych z dostępnością do ekspertów Lean. Powszechność Lean. Duzy wpływ na zwiększanie dojrzałości kultury organizacyjnej w kierunku Lean.
| Problemem może być ocena realizacji strategii Lean, rozmycie się jej realizacji w organizacji. Miernikiem zmian mogą być głównie zmiany w kulturze organizacyjnej uczelni, które są trudne do diagnozowania i mierzenia. Innymi miernikiem może być poziom satysfakcji, który z kolei jest miarą subiektywną. |
Dedykowany pracownik (stanowisko pracy ds. Lean) odpowiedzialny za wdrażanie koncepcji Lean plus formalny zespół/zespoły pracowników (Lean Team) plus wewnętrzna sieć specjalistów Lean oraz pracowników zainteresowanych CI | W organizacji tworzone jest stanowisko specjalisty ds. Lean, wpierany jest on przez zespół Lean oraz wewnętrzną sieć pracowników specjalistów Lean oraz pracowników zainteresowanych CI. | j.w. Duża powszechność i intensywność działań podejmowanych w związku z wdrażaniem strategii Lean. | j.w. |
Tabela 2 Rozwiązania organizacyjne wpierające proces wdrażaniu koncepcji Lean Management
Źródło: Maciąg J. (2019) Lean Culture in Higher Education. Towards Continuous Improvement. Palgrave Macmillan, Cham.
Rozwiązania organizacyjne wpierające proces wdrażaniu koncepcji Lean Management ewoluują w miarę wzrastania poziomu dojrzałości kulturowej i procesowej organizacji. Znane są przypadki organizacji, w których metody i narzędzia stały się sposobem realizacji codziennej pracy, integralną częścią kultury pracy pracowników i menedżerów, liderów zmiany. Nie potrzebują zatem już oni codziennego wsparcia w procesie doskonalenia. Wyspecjalizowane jednostki pomagają w realizacji dużych i przełomowych projektów o charakterze strategicznym.
Strategie wdrażania Lean w organizacji
Powszechnie strategia Lean jest definiowana i rozumiana w podejściu klasycznym jako kompleksowy plan realizacji celów w zakresie doskonalenia działania organizacji w oparciu o zasady Lean Management[50]. Jest strategia planowana, która stanowi integralną część wizji, misji oraz strategii rozwoju organizacji. Podejście do jej tworzenia oraz wdrażania zostało przedstawione na rysunku 1. Analiza doświadczeń różnych organizacji pokazuje, że obok klasycznej strategii planowanej wyłaniają się inne podejścia, wzorce zachowań i sposoby wdrażania filozofii Lean Thinking w organizacjach. Dlatego można wyróżnić klasyczne strategie planowane i wyłaniające się – emergentne. Strategie emergentne od strategii planowanych zadaniem Mintzberg i Waters odróżniają intencje, to w jaki sposób są artykułowane, czy można uznać je za organizacyjne oraz czy działania zostaną zgodnie z tymi intencjami zrealizowane[51]. Strategie emergentne wyłaniają się jako nieplanowane działania, które ewoluują z przeszłych doświadczeń lub nowo rozpoznanych wzorców w środowisku biznesowym[52].
Zatem mechanizm tworzenia się i realizacji strategii Lean może nie mieć zawsze charakteru zaplanowanego, celowego, odgórnego i linearnego. Prowadzone badania pozwalają na zdefiniowanie 5 rodzajów strategii Lean[53]:
- Strategia totalna
- Strategia adwokata,
- Strategia bocznych drzwi,
- Strategia wirusowa,
- Strategia kapiącej wody
Strategia totalna
Strategia totalna dominuje głównie w biznesie, ale można ją też odnaleźć w organizacjach publicznych, czy pozarządowych. Zmiana jest inicjowana przez naczelne kierownictwo organizacji oraz przy jego silnym wsparciu i zaangażowaniu wdrażana. Konwencjonalne przywództwo silnie ewoluuje w kierunku szczupłego przywództwa. Stosowane jest podejście odgórne z silną aktywizacją pracowników. Zwykle system Lean Management jest dobrze zorganizowany, wspiera pracowników i liderów zespołów. Organizowane są szkolenia. Badania wykazały, że strategia ta może być postrzegana przez menedżerów i pracowników jako strategia opresyjna. Często też zbyt duży nacisk położony jest na kwestie kosztowe i ekonomiczne, zaniedbując jednocześnie zmianę społeczną. Dlatego zasada okazywania szacunku i angażowania odgrywa kluczową rolę w osiąganiu sukcesu w procesie doskonalenia procesów i systemu zarządzania oraz budowaniu kultury Lean
Strategia adwokata
Strategia adwokata jest to strategia emergentna. Przyjmuje zazwyczaj następującą postać: w organizacji jest co najmniej jeden przedstawiciel naczelnego kierownictwa, entuzjasta Lean, który promuje i wspiera koncepcję, zapewniając dostępność zasobów niezbędnych do jej realizacji. Strategia Lean jest negocjowana z menedżerami najwyższego szczebla i zawsze jest formą kompromisu. Następnie, poprzez formalną i nieformalną sieć wewnętrznych liderów Lean, rozwijane są ich szkolenia, projekty i różne formy promocji. Kultura Lean rozszerza swój zasięg w organizacji. Zwykle ta emergentna strategia przenosi się na scentralizowaną strategię instytucjonalną i staje się strategią planowaną – strategią totalną. Strategia ta zazwyczaj opiera się na jednym charyzmatycznym liderze, który odgrywa kluczową rolę w kreowaniu zaangażowania na rzecz zmian. Gdyby ta osoba opuściła organizację, istnieje niebezpieczeństwo ograniczenia wszelkich inicjatyw Lean. Zagrożeniem jest również, sytuacja, w której lider-adwokat uzyskując zgodę i legitymizację swoich działań zaczyna narzucać rozwiązania bez ich wcześniejszej konsultacji.
Strategia bocznych drzwi
Strategię bocznych drzwi to strategia emergentna. Obierają menedżerowie średniego szczebla zarządzania, pracownicy na samodzielnych stanowiskach i inni. Wykorzystują oni metody i narzędzia Lean do zmiany podległych im procesów lub miejsca pracy. Zmiany ograniczają się zazwyczaj do jednego wydziału, jednostki, stanowiska ze względu na brak zaangażowania innych jednostek w organizacji. Czasami strategia ta może przenosić się na strategię instytucjonalną i scentralizowaną i staje się strategią planowana – strategia totalną. Oczekuje się, że z czasem działania oddolne zmuszą najwyższe kierownictwo organizacji do zmiany nastawienia do koncepcji Lean. Jeśli idea Lean nie przekroczy granic jednego wydziału, jednostki, procesu czy stanowiska i nie uzyska zaangażowania naczelnego kierownictwa, istnieje niebezpieczeństwo demotywacji ludzi, którzy w konsekwencji mogą zwrócić się na przeciwną stronę do jakichkolwiek zmian w organizacji lub ją opuścić. Osoba, próbująca dokonać zmian może spotkać się z ostracyzmem środowiska, gdyż działa wbrew tradycji, burzy dotychczasowe relacje, sieje ferment, zmusza do autorefleksji nad pracą, narusza status quo. Jej działania mogą w przyszłości skutkować zmianami, których ludzie się obawiają.
Strategia wirusowa
Strategia wirusowa to strategia emergentna. Istotą tej strategii jest dzielenie się wiedzą, kompetencjami i doświadczeniami poprzez nieformalną komunikację. Ludzie zaczynają mówić o Lean, używają wyrażenia Lean w codziennych rozmowach, a czasami żartują o Lean. Strategia ta wzbudza zainteresowanie wśród ludzi, aktywizuje ich, wyrywa z codziennej rutyny i czyni ich pracę bardziej sensowną i racjonalną. Strategia wirusowa jest nieodłączną częścią każdej z wymienionych powyżej strategii Lean. Dlatego dla menedżerów ważna jest świadomość istnienia takiego mechanizmu. Strategia ta może wzmocnić działania podjęte w planowanej strategii Lean lub przyczynić się do przekształcenia strategii adwokata i strategii bocznych drzwi w strategie totalne.
Strategia kapiącej wody
Strategia „kapiącej wody” to strategia emergentna. Może być z powodzeniem stosowana jako element pomocniczy we wszystkich wspomnianych strategiach. Woda wwierca się w skałę, tak że z czasem zmiany stają się nieodwracalne. Doświadczenie pokazuje, że w zasadzie po zakończeniu pierwszego projektu Lean każda osoba zaczyna inaczej patrzeć na procesy w organizacji, marnotrawstwo i możliwości zmian. Sposób myślenia i nastawienie takiej osoby zmieniają się bezpowrotnie. Często ludzie w pierwszym zetknięcie się z Lean odrzucają ta koncepcję, po czasie jednak zaczynają stosować pewne rozwiązania uważając je za użyteczne. Ta strategia wymaga czasu i cierpliwości.
Podkreśla się, że żaden podmiot realizujący kompleksową strategię Lean nie traktuje siebie i swojej aktywności jako stałej konstrukcji, maszyny do realizacji założonych wyników. Odchodzi się od podejścia, w którym punkt ciężkości jest położony na doskonałym planowaniu strategicznym a potem realizacji planów z wykorzystaniem najlepszych praktyk operacyjnych. Działalność jest postrzegana raczej jako dynamiczne zjawisko organiczne o ogromnym potencjale twórczym, które wypracowuje wzrost i samo się odnawia[54]. Punkt ciężkości jest położony na wdrażaniu opartym na elastyczności i samodzielności zespołów z wykorzystaniem techniki kaizen. To zespoły wspierane przez liderów wypracowują najlepsze metody realizacji misji organizacji.
Wykorzystanie Lean do realizacji celów zrównoważonego rozwoju
Nowe wyzwania przed jakimi stają organizacje związane są z przejściem w kierunku zrównoważonego zarządzania. W 2015 r. ONZ wyznaczyła 15 celów, które powinny być zrealizowane do 2030 r., aby uchronić ludzkość przed katastrofą klimatyczną[55]. Pojawia się coraz więcej publikacji wskazujących jak Lean Management możemy wykorzystać w realizacji celów zrównoważonego rozwoju[56]. Intensywnie rozwija się koncepcja Lean Green, która skupia się na likwidacji ekomarnotrastwa, bada się związki pomiędzy Lean Management a zrównoważonym rozwojem. Pojawiła się koncepcja Sustainable Lean Manufacturing. Wskazuje się, że następujące praktyki Lean management wpierają realizację celów zrównoważonego rozwoju w sferze środowiskowe, ekonomicznej i społecznej. Są to[57]:
- Wsparcie przez menedżerów i liderów
- Upełnomocnienie pracowników i współpraca
- Podejście systemowe
- Długoterminowe myślenie
- Eliminacja marnotrawstwa
- Nieustanne doskonalenie
- Tworzenie wartości
Koncepcja Lean dzięki wykorzystaniu potencjału ludzi w organizacji pozwala na wypracowanie modelu działania opartego na filozofii nieustannego uczenia się poprzez zespołowe rozwiązywanie problemów. Wyzwaniem jest budowanie społeczeństwa wolnego od marnotrawstwa.
Podsumowanie
Filozofia, metody i narzędzi Lean management wzbogacają instrumentarium zarządzania o perspektywę, która oparta jest na dogłębnym rozpoznaniu kontekstu i przyczyn generujących problemy w organizacji. Lean management uczy nas zauważać, dostrzegać i widzieć marnotrawstwo (learning to see) oraz daje nam bogate instrumentarium zmiany organizacyjnej. Jednak największym wyzwaniem we wdrażaniu Lean są stereotypy na temat tej koncepcji (np. drapieżna zmiana ukierunkowana na redukcję ilości pracowników). Wynikają one przede wszystkim z niezrozumienia jej istoty, a przede wszystkim zasad: nieustannego doskonalenia i szacunku dla ludzi. Lean management nie może być postrzegany tylko jako zbiór metod i narzędzi do wdrożenia szybkiej zmiany w wymiarze technicznym i organizacyjnym. Koncepcja ta posiada ogromny potencjał zmiany kultury organizacyjnej w kierunku nieustannego doskonalenia. Zmiana ta realizuje się poprzez zmianę postaw ludzi oraz ich kultury pracy. Warunkiem tej zmiany jest dobre zrozumienie fundamentalnych zasad Lean, wsparcie organizacyjne oraz nieustanne szkolenia.
Przypisy:
[2] Czerska, J. (2009). Doskonalenie strumienia wartości. Warszawa: Difin, s. 1-16.
[3] Bednarek, M. (2007). Doskonalenie systemów zarządzania. Nowa droga do przedsiębiorstwa Lean Warszawa: Difin, s. 33.
[4] Maciąg, J., Bugdol, M., & Peter-Bombik, K. (2021). Metody i narzędzia wdrażania Lean Management: poradnik dla menedżerów i pracowników szkół wyższych. Poltext. https://www.researchgate.net/publication/354814252_Metody_i_narzedzia_wdrazania_Lean_management_Poradnik_dla_menedzerow_i_pracownikow_szkol_wyzszych
[5] Krafcik, J. F. (1988). Triumph of the lean production system. Sloan management review, 30(1), 41-52.
[6] Womack, J. P., Jones, D. T., & Roos, D. (2008). Maszyna która zmieniła świat. ProdPress. com.
[7] Bicheno, J., & Holweg, M. (2016). The lean toolbox: A handbook for lean transformation (Vol. 5). Buckingham: PICSIE books.
[8] Bicheno, J., & Holweg, M. (2016). The lean toolbox: A handbook for lean transformation (Vol. 5). Buckingham: PICSIE books.
[9] Hamrol, A., Gawlik, J., Skołud, B. (2015). Strategie i praktyki sprawnego działania: Lean, Six Sigma i inne. Warszawa: Wydawnictwo Naukowe PWN, s. 99; Walentynowicz, P. (2013). Uwarunkowania skuteczności wdrażania Lean Management w przedsiębiorstwach produkcyjnych w Polsce. Gdańsk: Wydawnictwo Uniwersytetu Gdańskiego.
[10] Womack, J. P., Jones, D. T., & Roos, D. (1990). The machine that changed the world: The story of lean production. New York: Rawson Associates, 85.
[11] Maciąg, J. (2010). System zarządzania jakością usług : zasady i metody : (na przykładzie usług turystycznych i rekreacyjnych) (p. 243). Wydawnictwo Akademii Wychowania Fizycznego im. Jerzego Kukuczki. https://www.researchgate.net/publication/338912961_System_zarzadzania_jakoscia_uslug_zasady_i_metodyna_przykladzie_uslug_turystycznych_i_rekreacyjnych
[12] Bicheno, J., & Holweg, M. (2016). The lean toolbox: A handbook for lean transformation (Vol. 5). Buckingham: PICSIE books.
[13] Antony, J., Douglas, J., & Douglas, A. (2015). Waste identification and elimination in HEIs: the role of Lean thinking. International Journal of Quality & Reliability Management.
[14] Krafcik, J. F. (1988). Triumph of the lean production system. Sloan management review, 30(1), 41-52.
[15] https://en.wikipedia.org/wiki/Interchangeable_parts (dostęp 23.04.2022)
[16] Lean Foundation. Yellow Belt. University of Winchester; Liker J. K. (2018). Droga Toyoty. 14 zasad zarządzania wiodącej firmy produkcyjnej świata. MT Biznes, s. 55.
[17] Griffin, R. W., (2015). Podstawy zarządzania organizacjami. Wydawnictwo Naukowe PWN. Warszawa, s. 42-43.
[18] Gilbreth L.M., Emiliani B. (2019), Eliminating Waste in Teaching. Timeless Lessons For Improving Teaching and Training. Cubic LLC, South Kingstown, USA, s. 3
[19] Liker J. K. (2018). Droga Toyoty. 14 zasad zarządzania wiodącej firmy produkcyjnej świata. MT Biznes, s. 49.
[20] Szerzej: Hamrol, A. (2007). Zarządzanie jakością z przykładami. Wydawnictwo naukowe PWN. Warszawa, s. 264 i nast.
[21] Lisiecka, K., & Burka, I. (2016). Lean Service w teorii i praktyce. Wydawnictwo Uniwersytetu Ekonomicznego.; Maciąg, J. (2010). System zarządzania jakością usług : zasady i metody : (na przykładzie usług turystycznych i rekreacyjnych) (p. 243). Wydawnictwo Akademii Wychowania Fizycznego im. Jerzego Kukuczki. https://www.researchgate.net/publication/338912961_System_zarzadzania_jakoscia_uslug_zasady_i_metodyna_przykladzie_uslug_turystycznych_i_rekreacyjnych
[22] Latzko, W. J., & Saunders, D. M. (1998). Cztery dni z dr. Demingiem. Nowoczesna teoria zarządzania, Wydawnictwa Naukowo-Techniczne, Warszawa.
[23] Imai, M. (2006). Gemba kaizen: zdroworozsądkowe, niskokosztowe podejście do zarządzania. Wydawnictwo MT Biznes.
[24] Maciąg, J. (2010). System zarządzania jakością usług : zasady i metody : (na przykładzie usług turystycznych i rekreacyjnych) (p. 243). Wydawnictwo Akademii Wychowania Fizycznego im. Jerzego Kukuczki. https://www.researchgate.net/publication/338912961_System_zarzadzania_jakoscia_uslug_zasady_i_metodyna_przykladzie_uslug_turystycznych_i_rekreacyjnych
[25] Hamrol, A. (2007). Zarządzanie jakością z przykładami. Wydawnictwo naukowe PWN. Warszawa
[26] Ohno, T. (2008). System produkcyjny toyoty. Więcej niż produkcja na dużą skalę, ProdPress. com, Wrocław.
[27] Liker J. K. (2018). Droga Toyoty. 14 zasad zarządzania wiodącej firmy produkcyjnej świata. MT Biznes, s. 49 i nast.
[28] Lisiecka, K., & Burka, I. (2016). Lean Service w teorii i praktyce. Wydawnictwo Uniwersytetu Ekonomicznego, s. 19.
[29] Womack, J. P., Jones, D. T., & Roos, D. (2008). Maszyna która zmieniła świat. ProdPress. com.
[30] Womack, J. P., Jones, D. T., & Roos, D. (2008). Maszyna która zmieniła świat. ProdPress. com.
[31] Liker J. K. (2018). Droga Toyoty. 14 zasad zarządzania wiodącej firmy produkcyjnej świata. MT Biznes, s. 61
[32] Liker J. K. (2018). Droga Toyoty. 14 zasad zarządzania wiodącej firmy produkcyjnej świata. MT Biznes
[33] Bicheno, J., & Holweg, M. (2016). The lean toolbox: A handbook for lean transformation (Vol. 5). Buckingham: PICSIE books.
[34] Makkar, U., Gabriel, E., Tripathi, S.K. (2008). Value chain for higher education sector-case studies of India and Tanzania. Journal of Services Research, Special Issue, February 2008, s. 183.
[35] Leksykon Lean (2010), Wrocław, Lean Enterprise Institute, Polska, 2010.
[36]Ohno, T. (1988). Toyota production system: beyond large-scale production. crc Press.
[37] Douglas, A., Douglas, J., Antony, J. (2013). Gold in the Mine: Recognising Waste in UK HEIs using Lean Thinking. In: Enhancing Process Efficiency and Effectiveness in Higher Education Using Lean Six Sigma. In Proceedings of First International Conference on Lean Six Sigma for Higher Education. 24-25th June, 2013, Glasgow, Scotland, UK (electronic material), s. 22. Douglas, J., Antony, J., & Douglas, A. (2015). Waste identification and elimination in HEIs: the role of Lean thinking. International Journal of Quality & Reliability Management, 32(9), 970-981.
[38] Radnor, Z., Walley, P., Stephens, A. and Bucci, G. (2006), Evaluation of the Lean Approach to Business Management and its use in the Public Sector, Scottish Executive Social Research
[39] Radnor, Z., Walley, P., Stephens, A., Bucci, G. (2006). Evaluation of the lean approach to business management and its use in the public sector. Scottish Executive Social Research, 20, s. 62
[40] Starbird, D. (2017). The Value of a Lean Culture. The Journal for Quality and Participation, 39(4), 19; Emiliani, M.L. 1998. Lean behaviours. Management Decision, 36(9), 615-631 [Online]. Available: http://www.emeraldinsight.com/
[41] Hines, P., Holweg, M. & Rich, N. 2004. Learning to evolve. International Journal of Operations & Production Management, 24(10), 994-1011 [Online]. Available: http://www.emeraldinsight/ (accessed: 15 February 2008).
[42] Liker, J. K. (2005). The Toyota way. Esensi, s. 40.
[43] Atkinson, P., Nicholls, L. (2013). Demystifying lean culture change and continuous improvement. Management Services, 57(3), 10-15.
[44] Walentynowicz, P. (2013). Uwarunkowania skuteczności wdrażania Lean Management w przedsiębiorstwach produkcyjnych w Polsce. [The conditions for the effective implementation of Lean management in production enterprises in Poland.] Gdańsk: Wydawnictwo Uniwersytetu Gdańskiego; Mann, D. (2014). Creating a lean culture: tools to sustain lean conversions. Productivity Press.
[45] Zarbo, R. J. (2012). Creating and sustaining a lean culture of continuous process improvement; Miller, L. M. (2011). Lean Culture. The Leader‘s Guide. Annapolis, Maryland: LM Miller Consulting.
[46] Kusy, M., Diamond, M., & Vrchota, S. (2015). Why Culture Change Is Critical to Lean Initiatives. Lean training and coaching alone are not enough to improve customer satisfaction. Healthcare executive, 30(6), 48.
[47] Maciąg J. (2019) Lean Culture in Higher Education. Towards Continuous Improvement. Palgrave Macmillan, Cham.
[48] Maciąg J. (2019) Lean Culture in Higher Education. Towards Continuous Improvement. Palgrave Macmillan, Cham.
[49]Balle M., Jones D., Chaize J., Fiume O., Strategia Lean. Kultura uczenia się kluczem do budowania przewagi konkurencyjnej. MT Biznes. 2017
[50]Szerzej: D. Collis, Lean Strategy. Harvard Business Review MARCH 2016, https://hbr.org/2016/03/lean-strategy (dostęp 15.05.2018).
[51] Mintzberg, H., and Waters, J. A. (1985), “Of strategies, deliberate and emergent”. Strategic Management Journal, Vol. 6 No. 3, pp. 257-272.
[52] Bodwell, W. and Chermack, T. J. (2010), “Organizational ambidexterity: Integrating deliberate and emergent strategy with scenario planning”, Technological Forecasting and Social Change, Vol. 77 No. 2, pp. 193-202.
[53] Maciąg, J. (2021). Deliberate and emergent strategies of Lean implementation in Higher Education (HE)–a multiparadigmatic approach. Proceedings on the 8th International Conference on Lean Six Sigma, June 22-23.06.2021, Purdue University, West Lafayette, Indiana, USA, ed. Ch. Laux, J. Antony, S. O’Reilly, J. Healy. https://docs.lib.purdue.edu/iclss/
[54] Balle M., Jones D., Chaize J., Fiume O., Strategia Lean. Kultura uczenia się kluczem do budowania przewagi konkurencyjnej. MT Biznes. 2017, s. 357
[55] https://www.un.org.pl/ (dostęp 24.04.2022).
[56] Hartini, S., & Ciptomulyono, U. (2015). The relationship between lean and sustainable manufacturing on performance: literature review. Procedia Manufacturing, 4, 38-45.
[57] Klein, L. L., Alves, A. C., Abreu, M. F., & Feltrin, T. S. (2022). Lean management and sustainable practices in Higher Education Institutions of Brazil and Portugal: A cross country perspective. Journal of Cleaner Production, 130868.
Oceń ten artykuł:
Średnia ocen artykułu: / 5. Liczba ocen:
Brak ocen tego artykułu! Bądź pierwszym oceniającym.