Tymczasem kluczem do efektywności funkcjonowania firmy może być sprawny i efektywny przepływ wewnętrzny, skonstruowany tak aby wyeliminować zapasy międzyoperacyjne. Dlatego wszelkie usprawnienia procesów powinny koncertować się także na usprawnieniu procesu przepływu. Jednym z podstawowych narzędzi pozwalających na takie usprawnienie jest Kanban.
Spis treści
Kanban - narzędzie Lean Manufacturing
Źródła systemu Kanban należy poszukiwać, przede wszystkim, w koncepcji stworzonej przez Taiichi Ohno, długoletniego pracownika i w końcu prezesa Toyota Motor Company. Taiichi Ohno podzielił wszystkie działania realizowane w przedsiębiorstwie na dwie grupy: przynoszące wartość i nie przynoszące wartości. Działania przynoszące wartość to te za które chce zapłacić klient, natomiast operacje nie przynoszące wartości to operacje zbędne, które w dalszym ciągu należy wyeliminować. Koncepcję tą Taiichi Ohno opisał w książce Toyota Produktom System. W niej to Taiichi Ohno nazwał operacje nieprzynoszące wartości siedmioma wielkimi stratami w produkcji (7 MUDA). Zaliczył on do nich: nadprodukcję, nadmierne zapasy, błędy i wady jakościowe, oczekiwanie, nadmierne przetwarzanie, zbędny transport, zbędny ruch [1].
Pojawia się jednak pytanie jaki związek ma Kanban z 7MUDA. Podstawowymi celami Kanban są:
- Wyeliminowanie oczekiwania.
- Ograniczenie nadmiernego przetwarzania.
- Znaczące ograniczenie zapasu komponentów [2].
W Kanban, to magazyn lub umyślny pracownik jest odpowiedzialny za dostarczanie materiału. Zadaniem pracownika produkcji jest wytwarzanie, na bazie dostarczanych mu komponentów. Ma on to robić bez zatrzymania niezbędnego na udanie się do magazynu celem pozyskania materiału. Jednocześnie zmienia się konstrukcja i rola magazynu. W tradycyjnych przedsiębiorstwach magazyn służy do przechowywania zapasu, za ciągłość procesu produkcyjnego odpowiada produkcja. W systemie Kanban, magazyn jest także odpowiedzialny za skompletowanie i dostarczenie materiału na produkcję. W związku z tym magazyny w przedsiębiorstwach wykorzysujących Kanban mają znacznie większe przestrzenie kompletacyjne. W nich to, bowiem dochodzi do kompletacji tak zwanych Kitów (ang. Kit) czyli zestawów części dostarczanych na dane stanowisko montażowe.
Kanban prowadzi także do ograniczenia nadmiernego przetwarzania. Ta Muda jest związana z wykorzystaniem w przedsiębiorstwach nieadekwatnych i nadmiernie zaawansowanych rozwiązań w porównaniu do wymagań danego procesu. Generalnie w przypadku Kanban stosuje się bardzo proste rozwiązania. Podstawą są tutaj karty Kanban, ale również stosuje się rozwiązania oparte o sygnały świetlne, tablice sterujące tzw. Andony oraz tablice Kanban. Wszystkie te rozwiązania oparte są o rozwiązania wizualne i analogowe. To znaczy nie wymagają bardzo zawansowanego IT.
Przyczyny powstawania zapasu międzyoperacyjnego
Podstawowym celem Kanban jest ograniczenie zapasu międzyoperacyjnego, czyli takiego który jest tworzony w procesie produkcji na różnych stanowiskach pracy. Podstawowymi przyczynami powstawania takiego zapasu są:
- Dokumentacja wewnętrzna tj. dokumenty przychodu i rozchodu materiałowego.
- Przeszacowane normy zużycia.
- Wielkość konfekcjonowanej partii dostawy.
- Wąskie gardła.
Dokumentacja wewnętrzna przychodu i rozchodu materiałowego. Dokumenty przyjęcia i wydania magazynowego zostały stworzone do ewidencji zużycia materiałów w produkcji. W związku z powyższym, nie pozwalają one na sterowanie poziomem zapasu na poszczególnych stanowiskach pracy. W rezultacie na tych stanowiskach gromadzona jest zbyt duża ilość zapasu, w porównaniu do bieżącego zapotrzebowania. W skrajnych przypadkach poziom zapasu międzyoperacyjnego na poszczególnych stanowiskach przekracza poziom zapasu w magazynie głównym.
Przeszacowane normy zużycia. Wielu pracowników ma także potrzebę „chomikowania” zapasu. Jest to rezultatem źle pojętej zapobiegliwości, w zabezpieczeniu procesu produkcji, materiałem. W rezultacie dochodzi do gromadzenia materiału na danym stanowisku. Materiał ten jest wydany na podstawie dokumentu RW. Oznacza to przyporządkowanie zapasu do określonego zlecenia produkcyjnego i zablokowanie go na danym stanowisku. Taki zapas „oczekuje”, choć mógłby obsługiwać inne zlecenia. W konsekwencji, przeniesienie zapasu na produkcję, powoduje także konieczność jego uzupełnienia na magazynie głównym. W ten sposób powstają zbędne zapasy.
Wielkość konfekcjonowanej partii dostawy. W wielu przedsiębiorstwach, obrót materiałem następuje w oparciu o podstawową jednostkę transportowa – paletę. Jest ona dowożona na stanowisko pracy i tam składowana. Jej zawartość to zapas, wykorzystywany przez dłuższy czas. Celem udrożnienia i przyspieszenia rotacji takiego zapasu, wiele firm decyduje się na zmianę palety na mniejsze opakowania lub gotowe i wyliczone co do sztuki zestawy, dostarczone pod określone zlecenie produkcyjne.
Wąskie gardła. Brak odpowiedniego bilansowania przepływu także powoduje powstawanie zapasu międzyoperacyjnego. Jest to skutek różnych wydajności urządzeń znajdujących się w jednej linii produkcyjnej. W systemie Kanban rozwiązano ten problem poprzez stworzenie tzw. Supermarketów, czyli magazynów międzyoperacyjnych. Komasują one wcześniej wspomniane różnice. Z nich tworzona jest pełna partia produkcyjna. W rezultacie eliminuje się jedno zlecenie produkcyjne, obsługując je z różnic przechowywanych w danym supermarkecie.
Wszystkie te przyczyny powstawania zapasu, a w konsekwencji sam zapas, może zostać skutecznie wyeliminowany przez Kanban.
Kanban w przedsiębiorstwie
Obecnie w przedsiębiorstwach funkcjonują dwie koncepcje produkcji – koncepcja ssania (ang. Pull) i koncepcja pchania (ang. Push). W przypadku koncepcji opartej na pchaniu, wytwarzana jest partia produktów, która następnie jest magazynowana, aż do momentu, kiedy zostanie zamówiona przez klienta. W systemie ssącym (ang. Pull) zamówienie klienta wywołuje reakcję, w postaci uruchomienia produkcji pod to zamówienie [1]– rysunek 1. Nie istnieje, w konsekwencji, konieczność gromadzenia zapasu wyrobu gotowego.
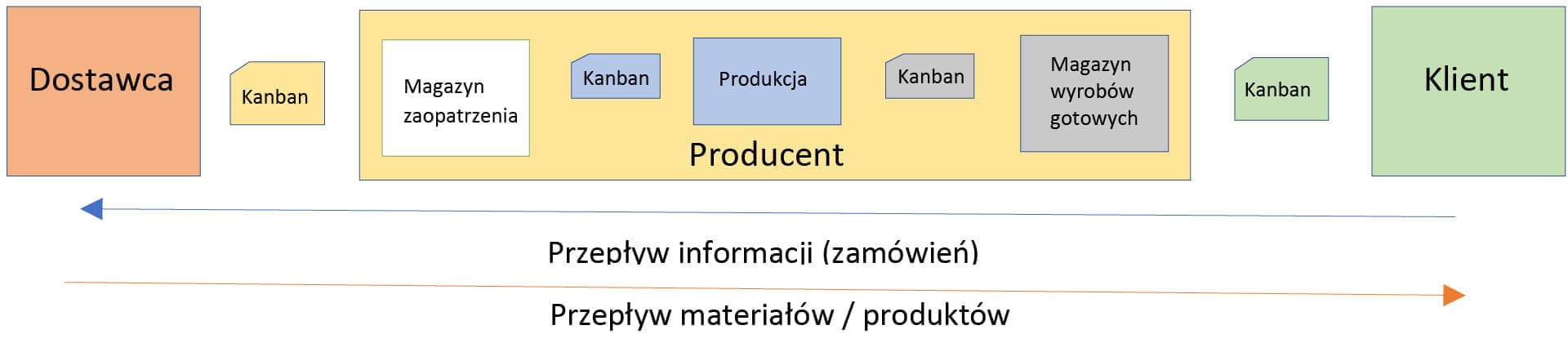
Zamówienie klienta wygenerowane zewnętrznym Kanbanem uruchamia, u producenta, dostawę obsługiwaną z magazynu wyrobów gotowych. Uzupełnienie zapasu na magazynie wyrobów gotowych następuje po wygenerowaniu i przesłaniu na produkcję kolejnej karty Kanban. Karta ta uruchamia produkcję wymaganej ilości wyrobu gotowego. Produkcja wysyła kolejną kartę Kanban celem uzupełnienia zapasu materiałowego w magazynie zaopatrzenia. Ubytek zapasu powoduje kolejne ssanie, pomiędzy magazynem zaopatrzenia a dostawcą[3].
Wprowadzenie systemu Kanban wymaga wyeliminowania całego szeregu ograniczeń. Część nich wynika z konieczności częstych przezbrojeń w procesie produkcji, inne konieczności zapewnienia stałej gotowości do realizacji dostaw oraz z wymagań wynikających z rytmicznego ssania klienta To ostatnie założenie jest związane z koniecznością odbioru przez klienta stałych, małych ilości wyprodukowanego wyrobu (rytmiczne ssanie)[4].
Rodzaje Kanbanów
W przedsiębiorstwie może jedocześnie wiele rodzajów Kanbanów[5]. Do najczęściej spotykanych rozwiązań należy:
- System dwupudełkowy,
- Wewnętrzny Kanban,
- Kanban na opakowania,
- Zewnętrzny Kanban.
System dwupudełkowy jest najprostszym Kanbanem, nie wymagającym tworzenia kart Kanban. Jest on stosowany w mniejszych przedsiębiorstwach, celem zarządzania dostawami materiałów bezpośrednio na produkcję. W tym systemie, materiał z jednego pudełka jest wykorzystywany w procesie produkcji, drugie pudełko stanowi zapas. W momencie, kiedy materiał z pierwszego pudełka zostanie wykorzystany, pracownik sięga po materiał z drugiego pudełka. Pierwsze puste pudełko wędruje w określone miejsce i zostaje zastąpione przez magazyniera pełnym pudełkiem. w rezultacie operator dysponuje zawsze dwoma pudełkami – jednym z którego wybiera materiał i drugim zapasowym. Pozom zapasu nigdy nie przekracza jednego pudełka.
Wewnętrzny Kanban jest to Kanban który łączy magazyn wyrobów gotowych z produkcją i produkcję z magazynem materiałów. Specjalnym rodzajem Kanban, nie odbiegającym jednak, w samej zasadzie działania, od pozostałych rodzajów Kanban, jest Kanban na opakowania. Łączy on magazyn opakowań z produkcją.
Stosunkowo rzadko stosowany jest zewnętrzny Kanban. Jest to Kanban łączący klienta z producentem lub producenta z dostawcą. Kanban w swojej zasadzie funkcjonuje bardzo podobnie jak Kanban wewnętrzny, przy czym zamówienie nie jest generowane przy pomocy dalej opisanej karty, lecz na drodze elektronicznej. Przykłady zewnętrznego Kanbanu można zaobserwować w takich firmach jak np. Valeo z Toyotą (wysyłka co osiem godzin kitu komponentów pod proces produkcyjny z Valeo do Toyoty) oraz Esselte ze swoim zewnętrznym magazynem.
Organizacja przepływu materiału przy pomocy Kanban
Organizacja systemu Kanban opiera się na trzech podstawowych zasadach. Pierwsza z nich zakłada regularność produkcji i powtarzalność operacji. Operacje, a także produkcja, musi zostać wykonywana w stałym i powtarzającym się czasie (ang. Takt time). Zapewnia to synchronizacje całego procesu produkcji. Takt time zapewnia także, że operator trafiając na kartę Kanban w pojemniku będzie miał wystarczającą ilość materiału, aby wytwarzać, aż z magazynu dostarczona zostanie kolejna dostawa. Oczywiście, należy przewidzieć tzw. Zapas bezpieczeństwa, więc uzupełnienie nie trafia w momencie, kiedy operator ma puste opakowanie, lecz kiedy posiada jeszcze kilka sztuk materiału, tak aby zapewnić nieprzerwaną pracę w chwili krótkiego spóźnienia dostawy.
Kolejna zasada to przepływ jednej sztuki (ang. One Piece Flow). Jest to metoda organizacji przepływu materiałów polegająca na przepływie tylko jednej sztuki poprzez całość ciągu technologicznego. W rezultacie minimalizuje się poziom zapasu, a także umożliwia produkowanie w sposób jak najbardziej płynny co jest podstawą utrzymania Takt Time.
Ostatnia trzecia zasada, dotyczy sposobu projektowania linii produkcyjnej pod Kanban. Optymalnym tutaj rozwiązaniem jest ułożenie jej w postaci linii prostej odpowiadającej logice procesu produkcji i kolejności czynności w procesie produkcji. Jednak z różnych względów, między innymi oszczędności miejsca, stosuje się linie produkcyjne w ułożone w kształcie litery U – rysunek 2.
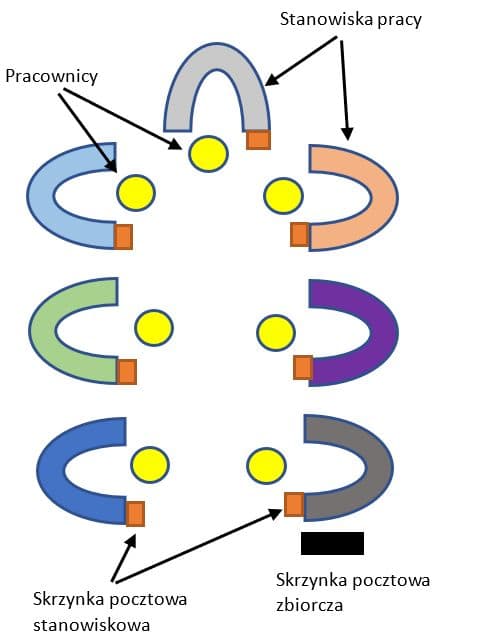
Na rysunku 2 przedstawiono, jeszcze jeden element często wykorzystywany w tego typu systemach, to jest produkcję opartą o tak zwane wyspy produkcyjne lub komórki produkcyjne (ang. Cell). Pracownik zaczyna od pierwszego miejsca wykonywania operacji na wyspie i przechodzi przez cały jej obszar, przechodząc z produktem pomiędzy miejscami, aż do osiągnięcia ostatniego miejsca operacji. Tam produkt jest zwykle testowany i przekazywany do dalej.
Pracownik wraca do pierwszego miejsca wykonywania operacji i rozpoczyna proces od nowa. Punkt początkowy i końcowy takiej wyspy powinny być zatem położony jak najbliżej siebie. Z tego powodu konstruuje się linie w kształcie litery U, a nawet litery Ω. O ile pozwala na to konstrukcja hal fabrycznych, linie U – kształtne, (zwane również Chaku-Chaku), są coraz częściej używane. Główne zalety takiego rozwiązania, w porównaniu z konwencjonalną produkcją przepływową, to:
- Wysoka elastyczność w odniesieniu do produkowanych odmian produktów,
- wysoka elastyczność w dostosowaniu ilości pracowników do wahań wielkości produkcji. Systemu U-kształtnym nie wszystkie miejsca w procesie produkcji muszą być obsadzone,
- skrócony czas dostawy, na skutek wyeliminowania oczekiwania na połączenie wielu wariantów,
- Ograniczenie poziomu zapasu międzyoperacyjnego, a tym samym zmniejszone zapotrzebowanie na przestrzeń składowania i zmniejszenie zamrożenia kapitału[6].
Podstawą całego systemu Kanban jest jednak Karta Kanban. Przykład takiej karty przedstawiono na rysunku 3.
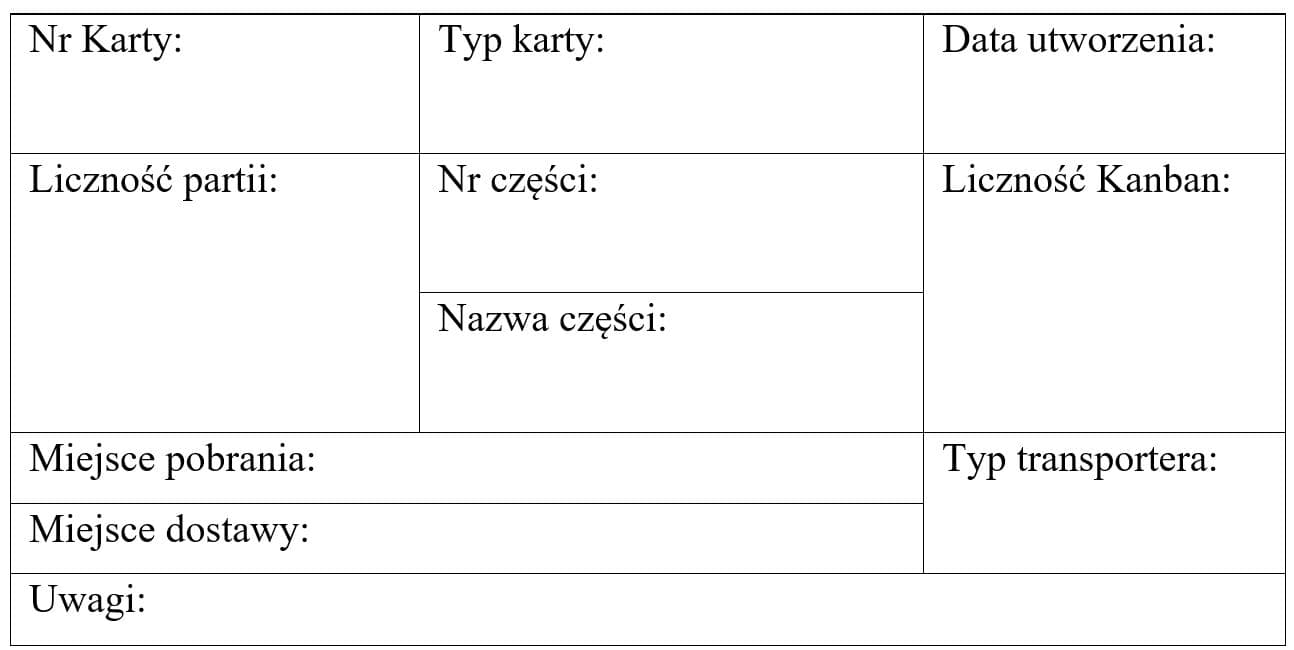
Karta taka jest umieszczona w pojemniku z materiałem lub jest przypięta do niego. Pracownik pobierający materiał, w pewnym momencie, trafia na nią i kolejno wrzuca ją do tak zwanej stanowiskowej skrzynki pocztowej. To uruchamia proces dostawy materiału na jego stanowisko, opisany szczegółowo w dalszej części. Liczba kart opisana jest wzorem:
Lk=\frac{Zk\ast C d\ast Z b}{Wp}
Gdzie:
Lk – liczba kart Kanban
Zk – zapotrzebowanie klienta – zapotrzebowanie na części (wyroby) w czasie (szt. / jednostkę czasu)
Cd – czas dostarczenia tj. suma czasu napełniania pojemnika, czasu realizacji zamówienia, czasu oczekiwania, czasu transportu
Zb – zapas bezpieczeństwa – dodatkowa ilość potrzebna do utrzymania produkcji w przypadku: awarii, problemów z jakością. Paramentr nie jest niezbędny do ustalenia liczby kart Kanban
Wp – wielkość partii – liczba części w pojemniku (lb szt / pojemnik).
Karty Kanban mogą mieć różne kolory. Kolory oznaczają poszczególne stanowiska lub linie (duże przedsiębiorstwa). W takich przedsiębiorstwach wózkowy dowożący materiał wywołany przy pomocy określonej karty podąża na dane stanowisko wzdłuż linii, w tej samej barwie co karta. To skraca transport. Kolorami mogą być także oznaczone typy Kanbanów – zewnętrzny, wewnętrzny.
W przedsiębiorstwach nie zawsze Kanban opiera się na kartach Kanban. Stosowany jest także Kanban oparty na sygnałach świetlnych. Ogólna zasada jest bardzo podobna, jak w przypadku klasycznego systemu Kanban. Pracownik, kiedy dociera do wyraźnie oznaczonego poziomu zapasu, włącza sygnał świetlny. Sygnał ten zapala się na magazynie identyfikując miejsce dostawy. Takie rozwiązanie najczęściej stosuje się w dostawach dużych komponentów[7].
W praktyce występuje jeszcze jeden rodzaj Kanbanu to jest Kanban wizualny. W przeciwieństwie do dotychczas opisanych rozwiązań, w tym zakresie, nie wykorzystuje on kart, lecz oznaczenia kolorystyczne. Malując kolorowe oznaczenia na ścianach, regałach i w innych miejscach określa on poziom maksymalny i minimalny zapasu oraz wywołuje w dalszej kolejności dostawę – rysunek 4.
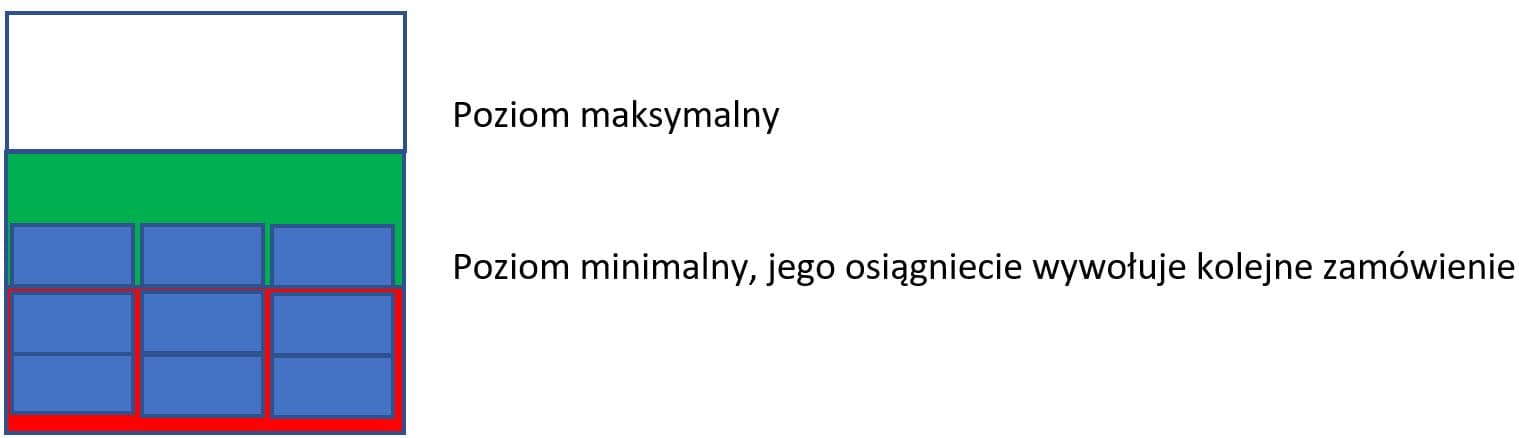
Jak zorganizować Kanban w przedsiębiorstwie?
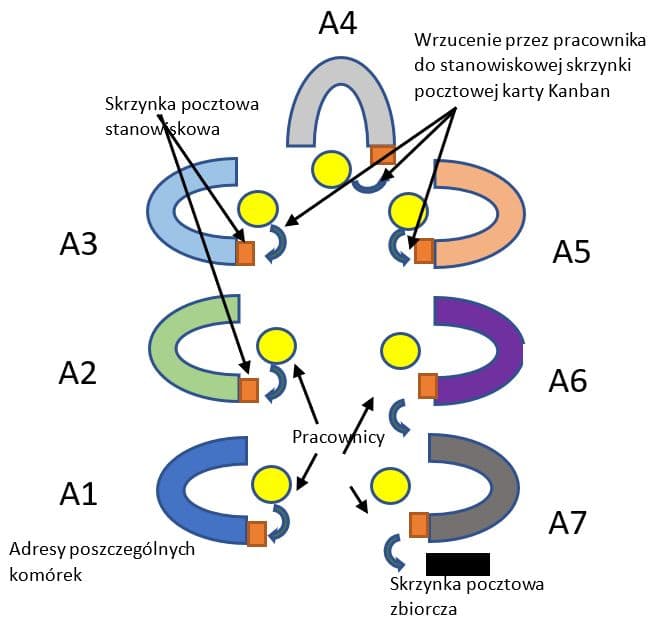
Karty te następnie są wyciągane z stanowiskowych skrzynek pocztowych i przekładane do zbiorczej skrzynki pocztowej. Kolejno karty ze zbiorczych skrzynek pocztowych są wyciągane przez tzw. „Gońca” i dostarczane do stanowiska skanowania. Jest to pewnego rodzaju odstępstwo od tradycyjnego Kanban, ale skanowanie jest niezbędne, ponieważ integrując się z systemem komputerowym, pozwala w skali całego przedsiębiorstwa, na planowanie dostaw materiałów oraz przyspiesza transfer informacji do magazynu – rysunek 6.
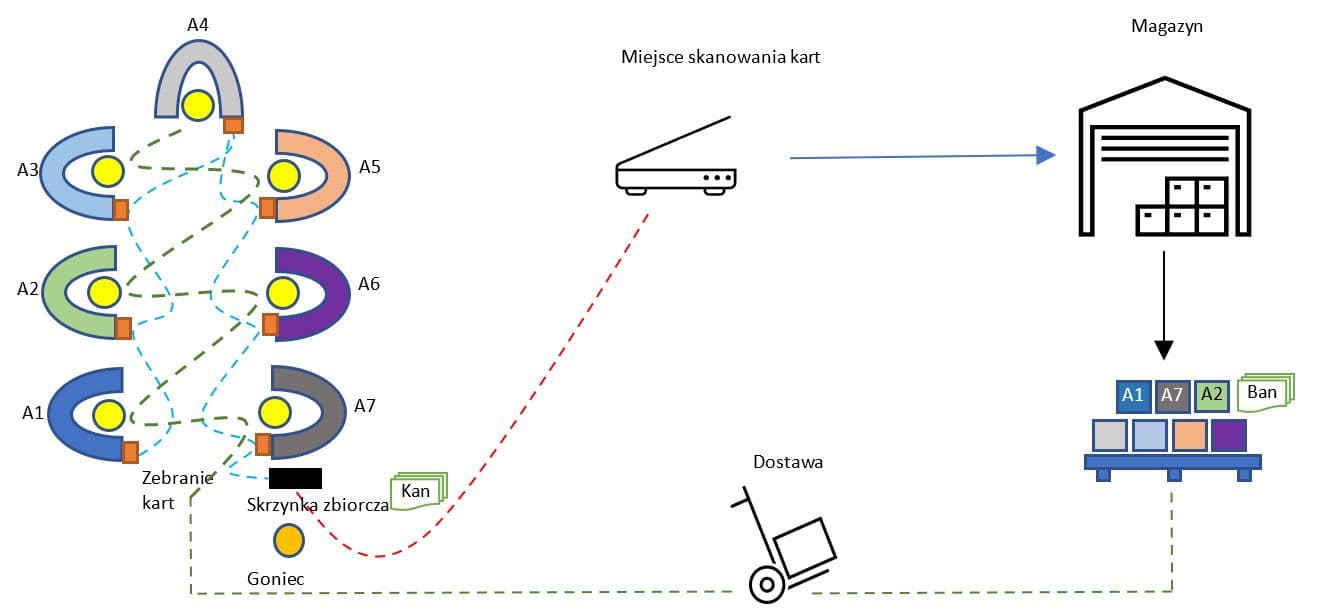
Ostatni krok to kompletacja. Jest ona przeprowadzona na podstawie kart Kan. Skompletowana dostawa wraz z kartami Ban (Zlecenie przepływu) jest dostarczona na linię. Pojemniki natomiast zostają dostarczone zgodnie ze swoimi adresami na poszczególne stanowiska.
Podsumowanie
Przypisy
[1] Truszkiewicz, B. (2014). Efektywna organizacja pracy linii produkcyjnych w koncepcji Lean Management. Contemporary Determinants of Economic Development, 289.
[2] Rahman, N. A. A., Sharif, S. M., & Esa, M. M. (2013). Lean manufacturing case study with Kanban system implementation. Procedia Economics and Finance, 7, 174-180.
[3] Arbulu, R., Ballard, G., & Harper, N. (2003). Kanban in construction. Proceedings of IGLC-11, Virginia Tech, Blacksburgh, Virginia, USA, 16-17.
[4] Zarychta, Z. (2013). Pull system jako innowacyjne rozwiązanie do sterowania produkcją. Prace Naukowe Wałbrzyskiej Wyższej Szkoły Zarządzania i Przedsiębiorczości, 25, 109-119.
[5] Esparrago Jr, R. A. (1988). Kanban. Production and Inventory Management Journal, 29(1), 6.
[6] Mak, P. (2016). Implementacja narzędzi Lean manufacturing w logistyce przedsiębiorstwa. Journal of TransLogistics, 2(1).
[7] Przybylska, E. (2013). Zastosowanie nowoczesnych rozwiązań w zaopatrzeniu materiałowym linii produkcyjnej przedsiębiorstwa. Zeszyty Naukowe. Organizacja i Zarządzanie/Politechnika Śląska.
[8] Budynek, M., Celińska, E., Dybikowska, A., Kozak, M., Ratajczak, J., Urban, J., Materne, K. (2016) Strategie sterowania produkcją jako narzędzia efektywnego zarządzania przedsiębiorstwem produkcyjnym. Management Systems in Production Engineering No 1(21),
[9] Arzet, Harry: Grundlagen des One Piece Flow. Berlin: Rhombos, 2005 – ISBN 3-937231-97-8. str. 7.
[10] Dziekoński, K., & Czepiel, P. (2014). Analiza funkcjonowania systemu Kanban w przedsiębiorstwie produkcyjnym. Zarządzanie przedsiębiorstwem, 17(1).
Oceń ten artykuł:
Średnia ocen artykułu: / 5. Liczba ocen:
Brak ocen tego artykułu! Bądź pierwszym oceniającym.