Spis treści
5S – skąd się wzięło? czyli etiologia 5S w skrócie
Analizując etiologię 5S należy wskazać trzy źródła pochodzenia tej koncepcji. Pierwszym z nich jest z pewnością ergonomia pracy. Czyli dyscyplina nauki zajmująca się przystosowaniem narzędzi, maszyn, środowiska pracy do psychofizycznych i anatomicznych możliwości człowieka [1]. Podstawowym celem Ergonomii pracy, podobnie jak 2S jest takie zaprojektowanie stanowiska pracy, aby zwiększyła się produktywność i wydajność pracownika. Kolejnym źródłem koncepcji 5S jest Zarządzanie jakością (ang. Total Quality Management) a właściwie cykl PDCA zdefiniowany przez Williama Edwardsa Deminga. Cykl ten realizowany jest czterech krokach: Zaplanuj (ang. Plan), Wykonaj (ang. Do), Sprawdź (ang. Check) i Zastosuj (ang. Act). Analizując przebieg procesu wdrażania 5S zaobserwować można głęboką analogię do cyklu PDCA. W cyklu PDCA, podobnie jak w 5S, zakłada się bowiem, w pierwszym kroku analizę stanu istniejącego, zaplanowanie działania oraz pomiar rezultatów zmian. W kolejnym kroku wdrożenie działań w małej skali. W 5S zakłada się także ograniczone działanie – 5S na poszczególnych wydziałach, w biurze, magazynie. W kolejnym kroku analizuje się rezultaty i wyprowadza wnioski. Ostatni krok cyklu PDCA, podobnie jak ostatni krok 5S to wprowadzenie standardu procesu, który powinien być przez wszystkich przestrzegany.
Trzeciego źródła 5S można jednak dopatrywać się, przede wszystkim, w koncepcjach stworzonych przez Taiichi Ohno, długoletniego pracownika i w końcu prezesa Toyota Motor Company. Podzielił on wszystkie operacje realizowane w procesie produkcyjnym na dwie grupy: przynoszące wartość i nie przynoszące wartości. Operacje przynoszące wartość to te za które chce zapłacić klient, natomiast operacje nie przynoszące wartości to operacje zbędne, które w dalszym ciągu należy wyeliminować. Koncepcje te Taiichi Ohno opisał w książce swojego autorstwa – Toyota Production System. W tej publikacji Taiichi Ohno nazwał operacje nieprzynoszące wartości siedmioma wielkimi stratami w produkcji (7 MUDA). Zaliczył on do powyższych strat: nadprodukcję, nadmierne zapasy, błędy i wady jakościowe, oczekiwanie, nadmierne przetwarzanie, zbędny transport, zbędny ruch. [2]
Obszary wykorzystania i organizacja 5S w przedsiębiorstwie
- Gemba Kaizen – system sugestii pracowniczych mający na celu ciągłą poprawę procesu,
- Total Productive Maintenance (TPM) – zapobieganie awariom poprawa efektywności pracy urządzeń,
- Single Minute Exchange of Die (SMED) – przyspieszenie przezbrojenia,
- Poka Yoka – taka konstrukcja procesu, aby zapobiegać błędom
- Kanban – minimalizacja zapasu produkcyjnego
- Just in Time – minimalizacja zapasu w łańcuchu dostaw.
- Selekcja (jap. Seirei; ang. Sort, Organization), – W miejscu pracy (w magazynie, na stanowisku produkcji czy w biurze) znajdują się tylko niezbędne do pracy narzędzia i materiały. Wszystko inne jest usunięte, tak aby by koncentrować się tylko na wykonywanych czynnościach.
- Systematyka (jap. Seiton; ang. Simplify, Orderliness) – Wszystko ma swoje miejsce i wszystko powinno znajdować się we właściwej dla niego lokalizacji, tak aby by było dostępne do natychmiastowego użycia.
- Sprzątanie (jap. Seiso; ang. Scrub, Cleanliness) – Miejsce pracy powinno być czyste i estetyczne.
- Standaryzacja (jap. Seiketsu; ang. Standardized Cleanup) – Kluczowym jest utrzymanie pierwszych trzech zasad. Zasady te winny być ciągle przestrzegane.
- Samodyscyplina (jap. Shitsuke; ang. Sustain, Discipline) – Doprowadzenie do sytuacji, w której wszystkie 4 zasady stają się codzienną postawą każdego pracownika [3].
1S Serei - Selekcja
- Zdefiniować rzeczy potrzebne w danej lokalizacji.
- Podzielić rzeczy na potrzebne (zgodnie z ustaloną definicją) i niepotrzebne, i te ostatnie usunąć. [4] Rzeczy niepotrzebne oznaczamy tzw. czerwoną etykietą – rysunek 1.
- Wyznaczyć miejsce przechowywania rzeczy, które na danym stanowisku są niepotrzebne, ale mogą zostać wykorzystane w innym miejscu (tymczasowy magazyn materiałów z czerwoną etykietą).
- Opracować procedury eliminujące pojawianie się rzeczy zbędnych, uprzątniętych w ramach selekcji.
- Znaleźć przyczyny źródłowe pojawiania się zakwestionowanych rzeczy, stworzyć procedurę zapobiegającą ich pojawianiu się i ciągle monitorować sytuację.
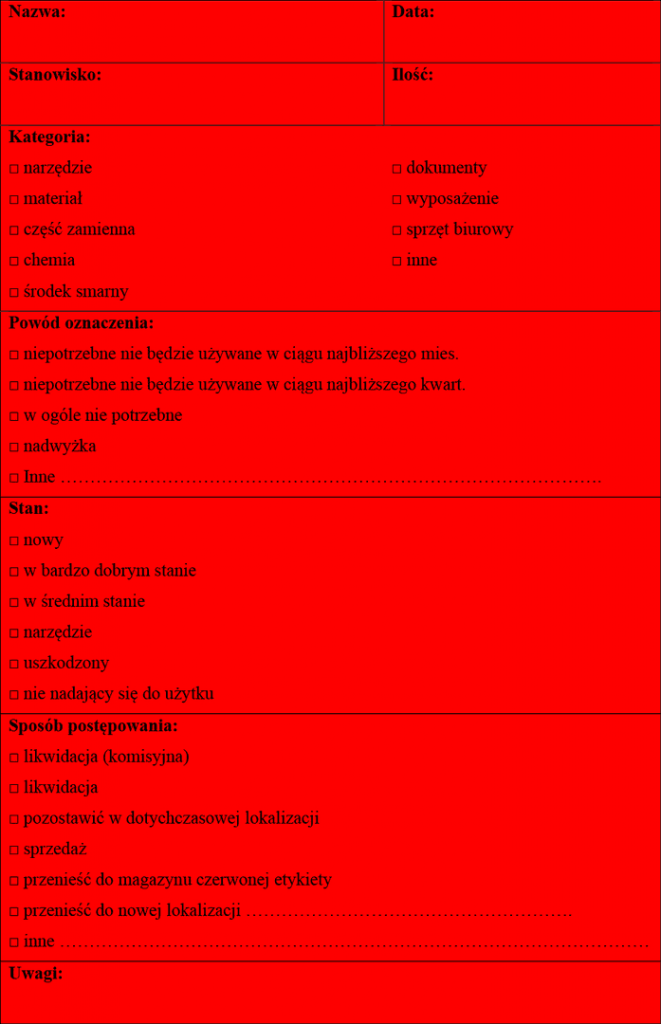
2S Seiton - Systematyka
Istotą 2S jest ustalenie i oznaczenie lokalizacji wszystkich przedmiotów wykorzystywanych na danym stanowisku. Wprowadzenie 2S wymaga:
- Umieszczenia wszystkich przedmiotów, części i materiałów w miejscach dla nich przeznaczonych.
- Zadecydowania, jak te przedmioty rozmieścić na stanowisku pracy.
- Wprowadzenia wizualnych środków do ich oznaczania i identyfikacji.
- Zdecydowania jak zostaną oznaczone limity ilościowe.
Należy tak zaprojektować stanowisko pracy, aby przedmioty na nim znajdujące się były łatwe do znalezienia, użycia i odłożenia. Aby określić lokalizację poszczególnych przedmiotów, a także zapewnić ich odkładanie we właściwe miejsca, można zastosować tzw. tablicę cieni. Nanosimy na stanowisko pracy obrys danego narzędzia lub obrys kuwety (pojemnika) z materiałem. Dane narzędzie/materiał powinno znajdować się zawsze wewnątrz swojego obrysu.
Wdrażając Systematykę należy przeanalizować po które przedmioty sięgamy najczęściej (grupa A), często (grupa B) i rzadko (grupa C). Następnie alokujemy przedmioty na stanowisku pracy zgodnie ze schematem przedstawionym na rysunku 2.
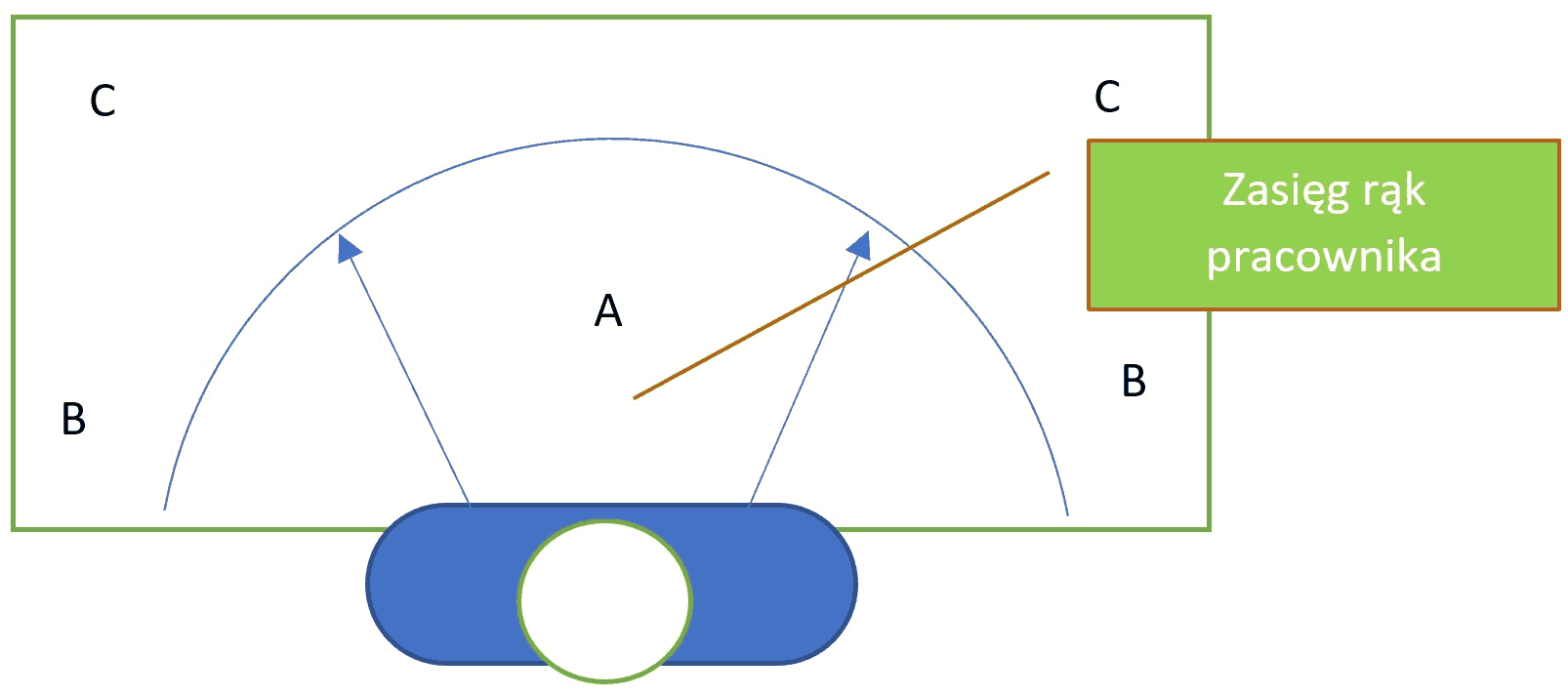
Wspomniany wcześniej system oznaczeń wizualnych pozwala także na skuteczne zarządzanie ilością materiałów, narzędzi i części. Jeśli oznaczymy jedno miejsce przechowywania (na przykład jedną kuwetę, jedną paletę, jeden klucz) to każda następna sztuka przechowywane poza danym obrysem będzie oznaczała nadwyżkę. W podobny sposób, malując kolorowe oznaczenia na ścianach, regałach i w innych miejscach możemy określać poziom maksymalny i minimalny zapasu oraz wywoływać w dalszej kolejności zamówienie – rysunek 3.
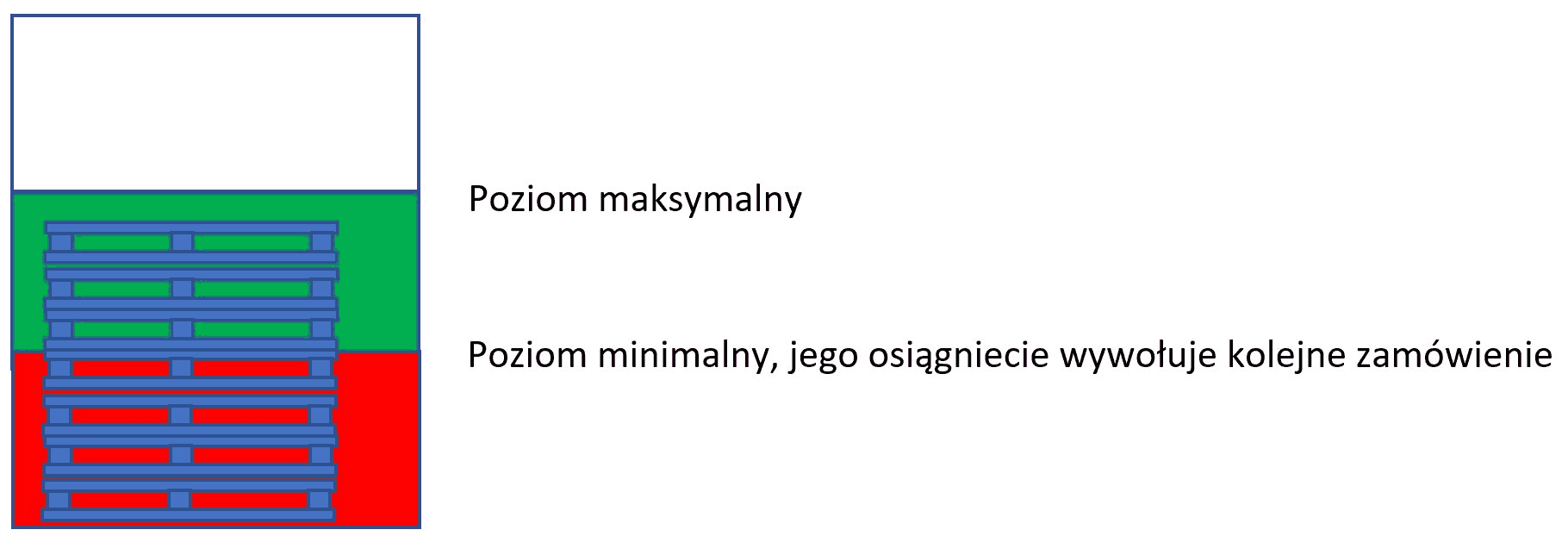
Jeśli liczba palet osiągnie poziom minimalny, to należy wysłać zamówienie do magazynu. Stanowisko ma zabezpieczony zapas palet na czas realizacji dostawy. W sytuacji, kiedy ostatnia paleta zostanie pobrana, magazyn powinien dostarczyć kolejne 8 palet, tak aby wypełnić pole czerwone i zielone. W ten sposób minimalizuje się poziom zapasu w miejscu pracy oraz zapewnia w sposób automatyczny ciągłość dostaw.
3S Seiso - Sprzątanie
Nadrzędnym celem Sprzątania jest utrzymanie w czystości stanowiska pracy, ale również znajdujących się na nim narzędzi, tak by były one natychmiast zdatne do pracy. Uprzątnięte stanowisko pracy pozwala na wizualną kontrolę i łatwe wychwycenie nieprawidłowości na stanowisku. Aby wprowadzić 3S należy:
- Usunąć brud i kurz na stanowisku pracy.
- Przeglądnąć i zidentyfikować a w końcu usunąć (jeśli jest to możliwe) źródła zanieczyszczeń.
- Poprawić czyszczenie poprzez lepszą dostępność środków czyszczących.
- Przygotować harmonogramy czyszczenia.
- Wprowadzić standardy czyszczenia oraz monitorować stan czystości.
Kolejnym celem 3S wychwycenie zanieczyszczeń, które mogą stać się przyczyną wypadku – rysunek 4.
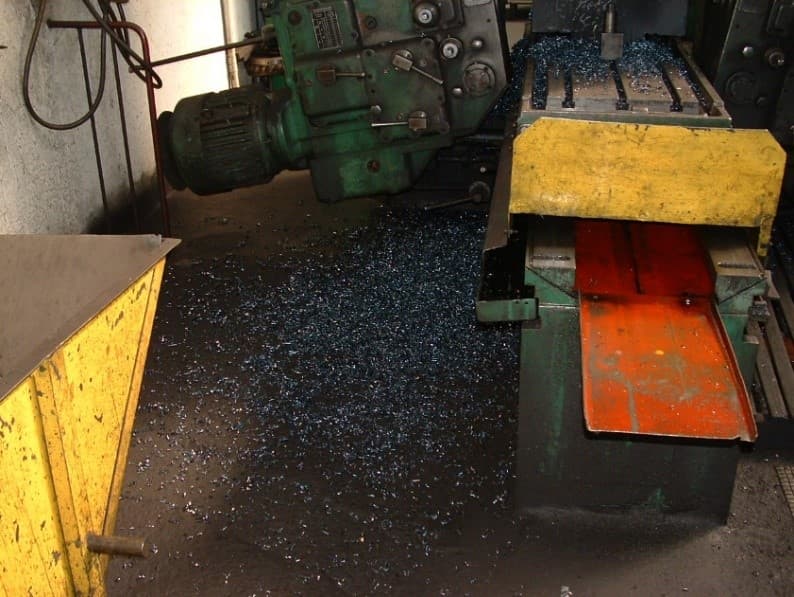
Przeprowadzony w przedsiębiorstwie audyt może, jak to przedstawiono na rysunku 4, wskazać miejsca, będące potencjalnymi miejscami powstawania wypadków. Powstająca przy tej okazji dokumentacja zdjęciowa, pozwala na wyegzekwowanie od odpowiedzialnych pracowników pożądanych zachowań.
Ostatnim celem 3S jest wychwycenie pierwszych (dyskretnych) objawów uszkodzenia urządzenia. Brud na stanowisku pracy, czy na posadzce, skutecznie maskuje potencjalne wycieki, olejów smarowniczych czy też olejów hydraulicznych, będące pierwszymi symptomami dużych awarii. Skuteczna interwencja w takiej chwili, jest w stanie zapobiec powstaniu dużej awarii, a w jej rezultacie zatrzymania urządzania lub całego ciągu technologicznego. Czyste miejsce pracy pozwala na szybką kontrolę wizualną a także na ustalenie przyczyn wycieku. Czyszczenie należy więc potraktować jako element prewencji i przeciwdziałania nieplanowanym zatrzymaniom urządzeń (awariom).
4S Seiketsu – Standaryzacja
Wdrożenie 1S-3S daje podstawę do wdrożenia 4S standaryzacji. Jest ona niczym innym jak opracowaniem procedur postępowań w ramach 5S. Aby wdrożyć 4S należy:
- Wprowadzić jasne instrukcje i opisy mówiące jak powinna wyglądać codzienna organizacja miejsca pracy lub czynności realizowane w miejscu pracy.
- Instrukcje powinny być napisana w zrozumiały sposób.
Przykład fragmentu instrukcji – tabela 1.
Przedmiot | Standard 5S | Częstotliwość konserwacji |
PALETA ZE ZŁOMEM | Zawsze stoi w wyznaczonym miejscu, obok tokarki. Palety na złom kolorowy i złom czysty stoją w wyznaczonych i podpisanych miejscach | Po napełnieniu odwozi wózkowy |
CZYŚCIWO | Stoi w izolatorze za blachą w rogu pomieszczenia | Nie porozrzucane, poukładane na swoim miejscu, odpowiedzialny pracownik x … |
MAUSER | Stoi tylko jeden, zapasowy mauzer jest dostarczony dopiero gdy bieżący się kończy | Pełny pojemnik wywieziony natychmiast po napełnieniu |
PRZESTRZEŃ WOKÓŁ URZĄDZENIA
| Podłoga wymyta myjką COMAX, nie ma porozrzucanych ścinków, wycieków oleju, szmat, pozbierane są wióry | Na bieżąco, pracownik x …
|
Tabela 2 Przykład fragmentu instrukcji utrzymania stanowiska pracy
W instrukcji wskazano obiekt, standard utrzymania oraz częstotliwość konserwacji. Wyznaczono także osobę odpowiedzialną za konserwację. Uzupełnieniem lub zamiennikiem instrukcji przedstawionej w tabeli 1 może być wzorzec wizualny. Wzorzec ten przedstawia idealnie utrzymane miejsce pracy. Najczęściej jest to więc fotografia wyczyszczonego i uporządkowanego miejsca pracy wraz ze stosownym komentarzem – rysunek 5
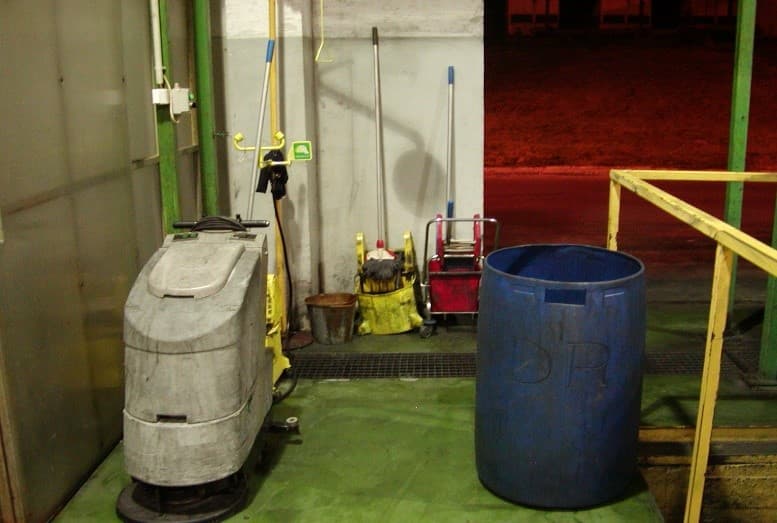
Miejsce przechowania mopów, myjka COMAX, naładowana i napełniona środkiem czyszczącym, pojemnik na czyściwo opróżniony, posadzka uprzątnięta, brak wycieków z myjki.
5S Shitsuke – Samodyscyplina
- Wsparcie – liderzy biorący udział audytach miejsc pracy, powinni uczyć i motywować pracowników do działania. Powinni także przeznaczać na to stosowne zasoby, również finansowe.
- Czas – wdrożenie 5S wymaga czasu. Schemat i czas wdrożenia można określić za pomocą harmonogramu wdrożenia 5S.
- Świadomość – działania i osiągnięcia 5S muszą być komunikowane wszystkim pracownikom, poprzez pokazywanie progresji przy pomocy ogólnodostępnych zdjęć, plakatów i wykresów.
- Nagrody i uznanie – wszystkie osiągniecia pracowników we wdrażaniu 5S powinny zostać nagrodzone
- Struktura – Należy określać, kiedy, w jaki sposób, powinny być wykonywane poszczególne czynności. Przydatnym tutaj narzędziem staje się wspomniany wcześniej harmonogram 5S [6]
Podsumowanie
Bibliografia
[1] https://encyklopedia.pwn.pl/szukaj/ergonomia%20pracy.html (13.04.2022)
[2] Bayo‐Moriones, A., Bello‐Pintado, A., & de Cerio, J. M. D. (2010). 5S use in manufacturing plants: contextual factors and impact on operating performance. International Journal of Quality & Reliability Management.
[3] Randhawa, J. S., & Ahuja, I. S. (2017). 5S–a quality improvement tool for sustainable performance: literature review and directions. International Journal of Quality & Reliability Management Pacana,
[4] Wolnowska, A. (2010). Praktyka wdrażania koncepcji 5S. Retrieved, 11, 2019.
[5] A., Gazda, A., & Wołoszyn, P. (2014). Wykorzystanie metody 5S do doskonalenia procesów logistycznych. Modern Management Review, 2, 73-80.
[6] Gundlach, M. (2009). Praktyki 5S jako pierwszy krok do wdrożenia produkcji odchudzonej w przedsiębiorstwie produkcyjnym. Rozwinięcie teorii 6S.
[7] Kamińska, A. (2016). Praktyczne zastosowanie 5S w wybranych fabrykach branży motoryzacyjnej. Studia Oeconomica Posnaniensia, 4(10).
[8] Łopatowska, J. (2002). Metoda 5S jako narzędzie modelowania procesów na stanowisku pracy.
Oceń ten artykuł:
Średnia ocen artykułu: / 5. Liczba ocen:
Brak ocen tego artykułu! Bądź pierwszym oceniającym.