Spis treści
Cykl nieustannego doskonalenia PDCA
Doskonalenie wszystkich działań i procesów poprzez systematyczne i metodyczne rozwiązywanie problemów powinno być stałym celem organizacji. Organizacja odnosząca sukcesy stale jest ukierunkowana na doskonalenie[1]. Jak podkreśla się w normie PN-EN ISO 9000:2015,
doskonalenie jest istotne dla organizacji w celu utrzymania bieżącego poziomu efektów działalności, możliwości reagowania na zmiany warunków wewnętrznych i zewnętrznych oraz w celu stwarzania nowych szans[2].
Metoda PDCA (koło Deminga), jest uniwersalną dyrektywą doskonalenia jakości usług, procesów oraz systemu zarządzania organizacją. Jest również uniwersalną dyrektywą stosowaną w cyku rozwiązywania problemu. Rysunek przedstawia ideę cyklu PDCA (Plan, Do, Check, Act) w procesie rozwiązywania problemu.
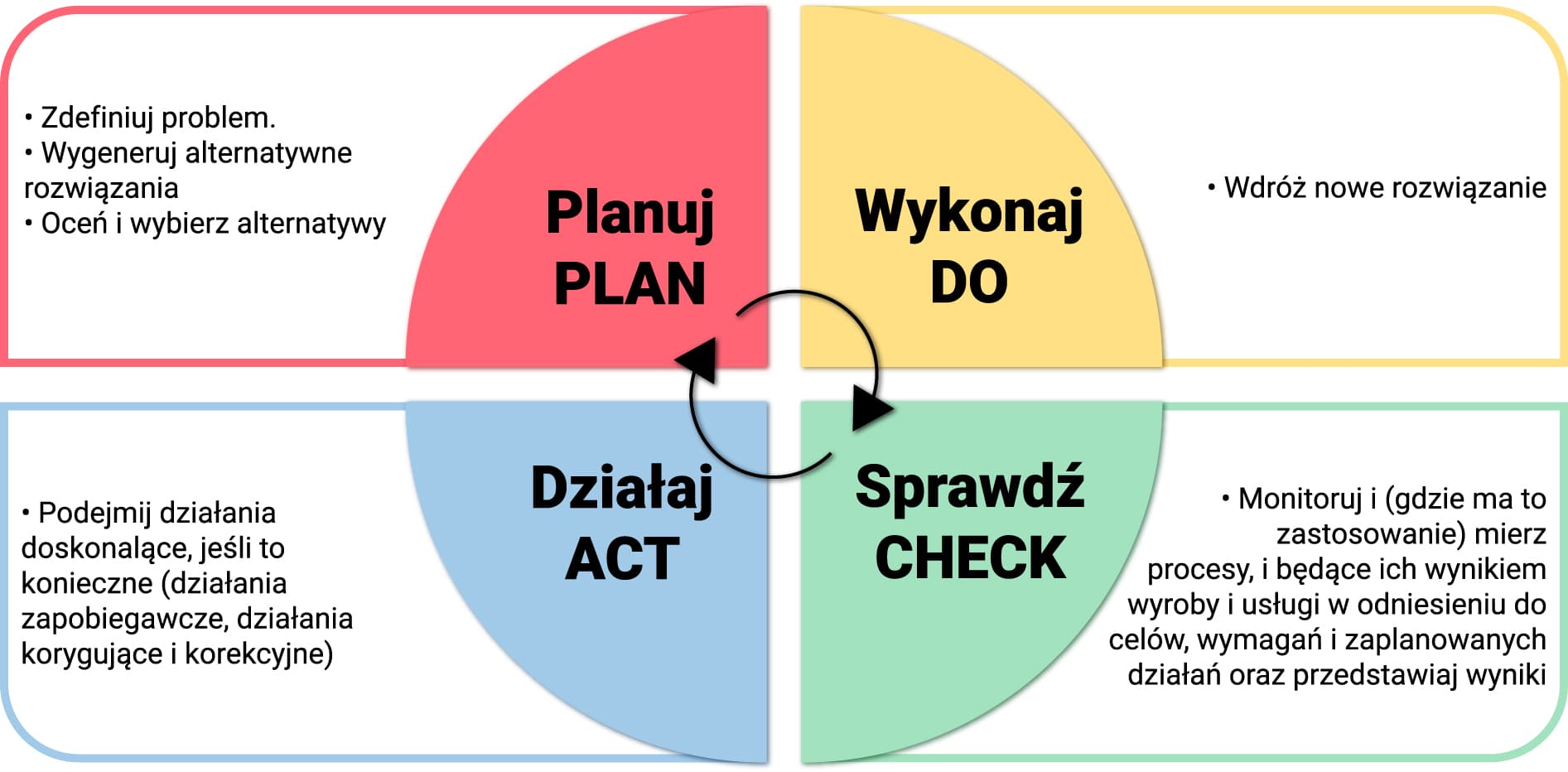
- działania zapobiegawcze – podejmowane w celu wyeliminowania przyczyny lub przyczyn potencjalnej niezgodności lub inne sytuacji niepożądanej w organizacji (działanie to jest podejmowane w celu zapobiegania sytuacjom, które mogłyby doprowadzić do niespełnienia wymagań w przyszłości);
- działania korygujące – podejmowane w celu wyeliminowania przyczyny lub przyczyn zaistniałej niezgodności i zapobieżeniu jej wystąpienia w przyszłości, podejmowane są one zazwyczaj po wystąpieniu problemu;
- działania korekcyjne – podejmowane są w celu usunięcia problemu, natomiast nie usuwają przyczyny jego wystąpienia np. naprawa urządzenia.
Techniki definiowania i określania alternatyw rozwiązań
5Whys
Technika 5Why’s jest niezwykle przydatną techniką na etapie definiowania problemu oraz określania jego pierwotnych przyczyn. polega na pięciokrotnym zadawaniu pytania dlaczego w celu zidentyfikowania relacji pomiędzy poszczególnymi przyczynami generującymi problem w procesach i działaniach organizacji/zespołu. Technika ta pierwotnie była częścią TPS (Toyota Production System) i po raz pierwszy została zastosowana w latach 50’ XX w. przez Sakichi Toyoda. Główną ideą techniki 5Whys jest unikanie sytuacji, w której zadowalamy się szybkimi rozwiązaniami problemów, a nie pogłębiamy analizy dalszymi szczegółowymi pytaniami. Dlatego jeśli istnieje taka potrzeba, to można zadać pytanie, dlaczego więcej niż 5 razy.
Etapy realizacji:
- Zdefiniuj problem
- Zadawaj pytania
- Podsumuj analizę
Główną zaletą 5Whys jest łatwość zastosowania, prostota, taniość, elastyczność, kreatywność oraz angażowanie zespołu w rozwiązywanie problemów. Istotna też jest depersonalizacja czyli skupienie się na problemie, a nie na ludziach. Technika 5Whys ma też pewne ograniczenia. Możemy uzyskiwać wiele odpowiedzi na postawione pytania, zatem istnieje konieczność przeprowadzenia wielu analiz, może być to złożonym wyzwaniem.
Poniżej umieszczono przykład wykorzystania.
Przykład wykorzystania metody 5 Whys
PROBLEM: Zbyt długi czas odpowiedzi na zapytanie ofertowe. Czas przygotowania odpowiedzi na zapytanie ofertowe wynosi od 5-14 dni. Oczekuje się, że odpowiedź zostanie przygotowana w ciągu mx. 3 dni.
Pytanie 1: Dlaczego odpowiedź na zapytanie ofertowe jest przygotowywana zbyt długo?
Gdyż bardzo długo trwał proces podpisywania pełnomocnictwa do złożenia oferty.
Pytanie 2: Dlaczego tak długo trwał proces podpisywania pełnomocnictwa do złożenia oferty.
Bo dokumenty są podpisywane przez kilka osób zgodnie z przyjęta hierarchią w strukturze organizacyjnej.
Pytanie 3: Dlaczego dokument jest podpisywany przez kilka osób?
Proces nie został zrestrukturyzowany.
Pytanie 4: Dlaczego proces nie był restrukturyzowany?
Bo kierownicy uważają, że nie ma takiej potrzeby.
Pytanie 5: Dlaczego kierownicy uważają, że nie ma potrzeby restrukturyzacji?
Bo są przyzwyczajeni do starych zasad, obawiają się zmian i wyjścia ze strefy komfortu.
Przyczyny: rutyna i brak odczuwania chęci i potrzeby zmian przez kierownictwo.
Działania: szkolenie dla kierowników z zakresie zarządzania procesami i Lean management, pokazanie korzyści zmian.
5W2H
Technika 5W2H jest podobna w swojej istocie do techniki 5Whys. Polega zebraniu jak największej ilości informacji i danych poprzez zadawanie zestawu pytań. Nazwa tej techniki pochodzi od ilości i rodzaju zadanych pytań (Tabela 2). Może być ona wykorzystana w analizie problemu lub do planowania zadań, działań i procesów oraz oczekiwanych rezultatów. Znajduje zastosowanie również w przygotowaniu dokumentów tj. procedury i instrukcje. W zależności od przeznaczenia zadawane są różne pytania.
Pytania | Analiza problemu | Plan działania |
What? | Co jest problemem? Czego on dokładnie dotyczy? Czy się powtarza czy jest jednorazowy? | Co powinnyśmy zrobić? Jakie są kroki, etapy działania? |
Who? | Kto zgłosił ten problem – klient, pracownik? | Kto wykona działania? Kto jest odpowiedzialny? Do kogo przekazać wyniki? Kto akceptuje? |
Where? | Gdzie on powstał? W jakim dziale, procesie? | Gdzie ma to być zrobione? |
When? | Kiedy miało miejsce? Na jakiej zmianie? O jakiej godzinie? Jakie są okoliczności? | Na kiedy mamy to zrobić? Jakie są terminy? |
Why? | Dlaczego jest to problem? Jakie są konsekwencje dla organizacji? Dlaczego ten problem powstał? Czy zostały złamane jakieś procedury czy instrukcje? Czy w ogóle takie istniały? | Po co my to robimy? Jaką tworzymy wartość? Kto jest naszym klientem? Jakie jest uzasadnienie biznesowe? |
How? | Jak zostało to odkryte? Jaki jest mechanizm powstawania takich problemów? Jakie są przyczyny? | Jak ma to być zrobione? Czy są jakieś standardy? Jakich użyjemy metod i technik? Jakich maszyn, urządzeń, oprogramowania? |
How much? How many? | Jak dużo? Jaka jest skala problemu? Jakie są to dla nas koszty? | Jakie są koszty? Jakie nakłady będą potrzebne? Jaka jest skala przedsięwzięcia? |
Tabela 2 Technika 5W2H. Źródło: opracowanie własne na podstawie: https://tqmsoft.com/pl/qnowhow/2017-07-27/5w2h-czyli-jak-dokladnie-opisac-problem; https://www.heflo.com/blog/process-mapping/5w2h-method-examples/
5W2H pozwala na posegregowanie i uporządkowanie informacji i danych niezbędnych do rozwiązania problemu zaplanowania działań. Ograniczeniem zastosowania tej techniki może być złożoność i kompleksowość podejmowanych zagadnień. Zagrożeniem jest też brak obiektywizmu oraz zbyt duża ogólnikowość i lakoniczność.
Diagram pokrewieństwa
- Zdefiniowanie analizowanego zagadnienia/problemu
- Zebranie pomysłów, idei, informacji i ich zapisanie (na kartkach)
- Uporządkowanie pomysłów, idei, informacji w grupy tematyczne (maksymalnie 10 grup)
- Wyznaczenie w danej grupie tematycznej problemu wiodącego.
- Prezentacja otrzymanych wyników
Diagram pokrewieństwa pozwala na kompleksową i holistyczną analizę problemu, biorąc pod uwagę różne punkty widzenia. Daje możliwość zanonimizowania odpowiedzi uczestników, co jest szczególnie ważne, przy rozwiązywania kontrowersyjnych i kłopotliwych z jakiś powodów problemów. Diagram pokrewieństwa może jednak nie sprawdzić się przy analizie zbyt dużych i skomplikowanych problemów. Wybór dominujących przyczyn analizowanego problemy lub zdarzenia ma charakter subiektywny, nie poparty analizami ilościowymi.
Poniżej zostanie zaprezentowany przykład wykorzystania Diagramu pokrewieństwa.
Przykład wykorzystania Diagramu pokrewieństwa
PROBLEM: Wzrasta poziom wypalenia zawodowego pracowników w organizacji.
Opis: W ciągu ostatniego roku:
- Maleje wskaźnik jakości życia w miejscu pracy (2020 – 4,0 do 2021 – 3,8, skala 1-5)
- Wzrasta wskaźnik absencji (2020 – ilość dni nieobecności - średnio 10 na 1 pracownika, 2021 – 14 dni na 1 pracownika)
- Wzrasta wskaźnik rotacji pracowników (2020 – 1%, 2021 – 1,5 %)
Metoda badania: diagram pokrewieństwa.
Zorganizowano spotkanie z pracownikami, poproszono o wypisane przyczyn wypalenia zawodowego, moderator we współpracy z pracownikami uporządkował przyczyny nadając nazwy wyłaniającym się jednorodnym kategoriom. Jako główne kategorie przyczyn wypalenia zawodowego wskazano: brak gratyfikacji/wynagrodzenia, skostniała struktura, błędy komunikacyjne, monotonie pracy, brak sprawczości, błędy w zarządzaniu zespołem, brak możliwości rozwoju oraz niewłaściwą organizację stanowiska pracy.
Należy zwrócić uwagę na fakt, że przyczyny mają charakter systemowy.
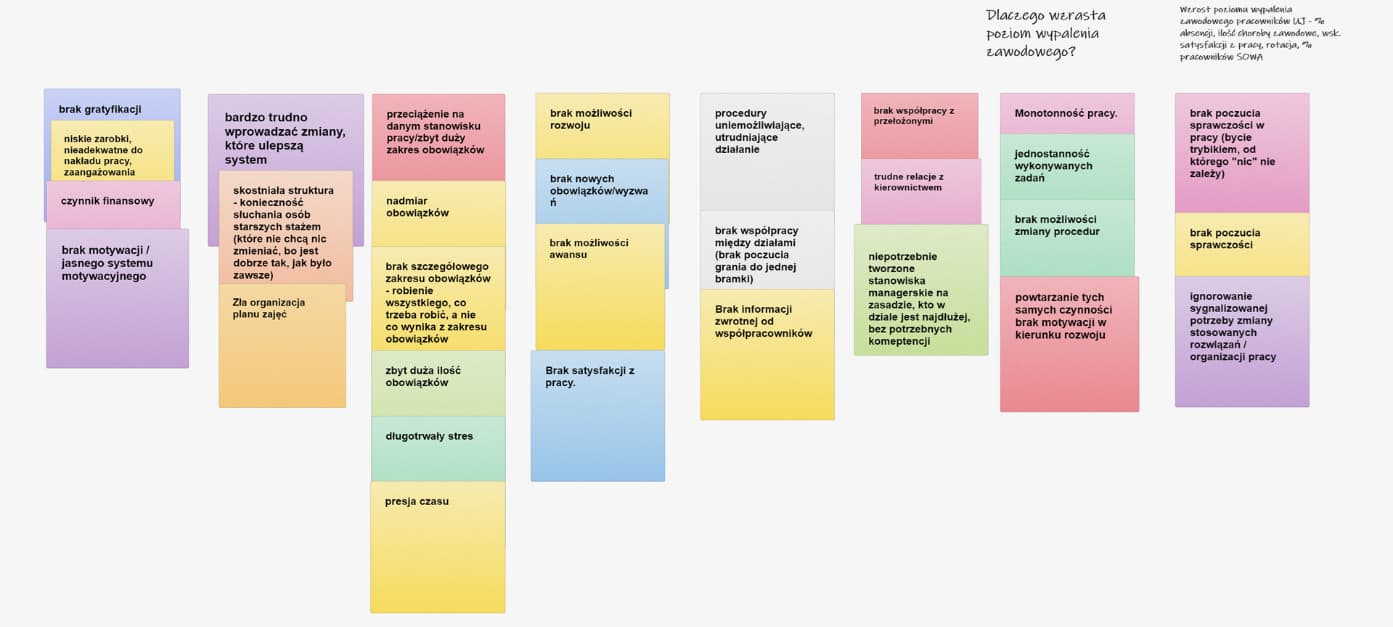
Wykres relacji
- Opisanie problemu jako centralnego węzła diagramu
- Wskazanie przyczyn wywołujących problem, tworzących pozostałe węzły diagramu
- Wskazanie wzajemnych powiązań pomiędzy przyczynami
- Wskazanie najważniejszych przyczyn
Poniżej przykład wykorzystania Wykresu relacji.
Przykład wykorzystania wykresu relacji
PROBLEM: Wzrasta poziom wypalenia zawodowego pracowników w organizacji.
Opis: W ciągu ostatniego roku:
- Maleje wskaźnik jakości życia w miejscu pracy (2020 – 4,0 do 2021 – 3,8, skala 1-5)
- Wzrasta wskaźnik absencji (2020 – ilość dni nieobecności - średnio 10 na 1 pracownika, 2021 – 14 dni na 1 pracownika)
- Wzrasta wskaźnik rotacji pracowników (2020 – 1%, 2021 – 1,5 %)
Wykorzystują diagram pokrewieństwa wskazano główne kategorie przyczyn wypalenia zawodowego. Są to:
- brak gratyfikacji/wynagrodzenia
- skostniała struktura
- błędy komunikacyjne
- monotonie pracy
- brak sprawczości
- błędy w zarządzaniu zespołem
- brak możliwości rozwoju oraz niewłaściwą organizację stanowiska pracy
Wykorzystując wykres relacji dokonano analizy zależności pomiędzy kategoriami przyczyn. Istnienie lub brak relacji ustalano poprzez udzieli odpowiedzi na pytanie czy dana przyczyna wpływa na inną przyczynę. Jeśli odpowiedź brzmiała tak to została na wykres naniesiona strzałka. Po przeprowadzeniu analizy wszystkich relacji policzono strzałki dochodzące do danej kategorii (WE) oraz odchodzące od danej kategorii (WY).
Wykres relacji pozwala na pokazanie, który z analizowanych czynników w największym zakresie wpływa na inne przyczyny problemu wskazane w analizie. Pozwala dzięki temu na wskazanie przyczyn pierwotnej oraz wskazanie przyczyn wtórnych. Jest to narzędzie analizy jakościowej, zatem dobór zespołu (zaleca się zespoły interdyscyplinarne), wybór przyczyn do analizy oraz właściwa analiza powiązań wpływają na rzetelność i wiarygodność wyników końcowych analizy.
Poniżej przedstawiono wyniki badania.
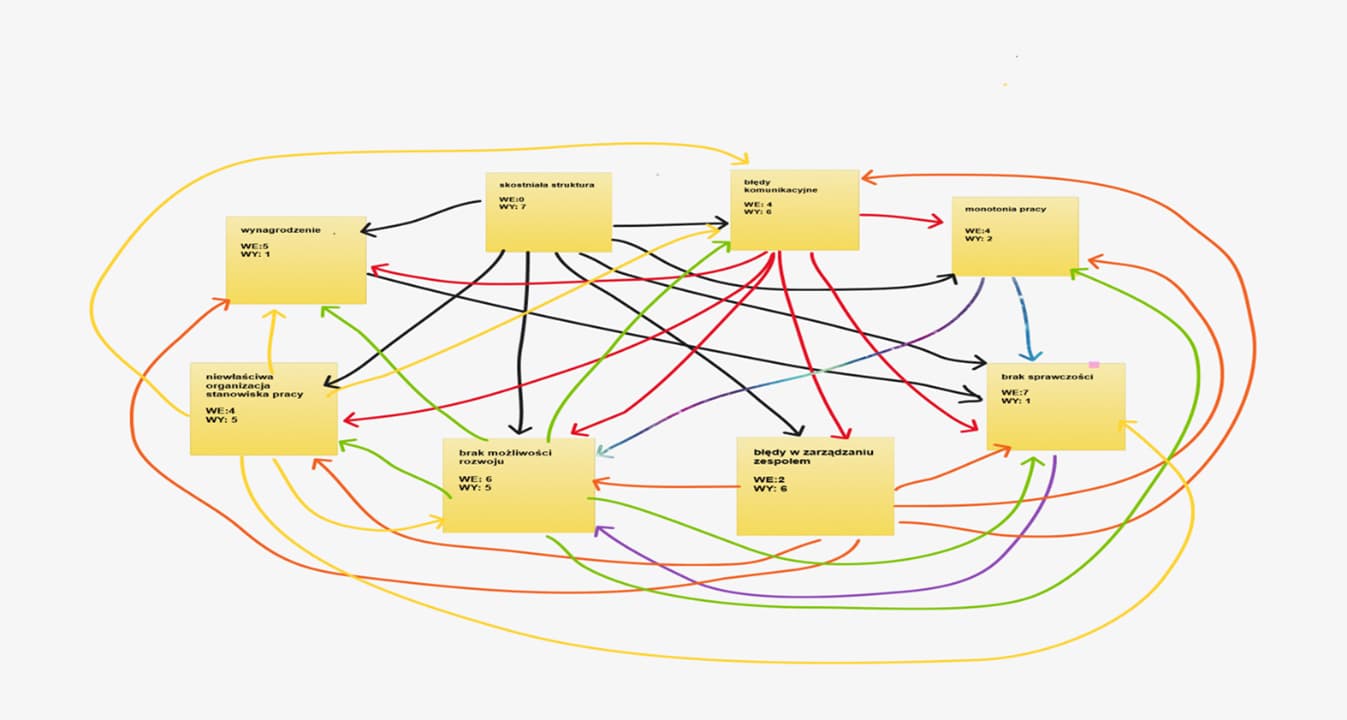
Do kategorii, które najsilniej wpływają na wypalenie zawodowe można zaliczyć:
- skostniałą strukturę WY 7
- błędy komunikacyjne WY 6 oraz błędy w zarządzaniu zespołem WY6
Wyniki badania wskazują, że problem związany z wypaleniem zawodowym kierownictwo organizacji powinno rozpocząć od działań restrukturyzacyjnych i doskonalących w zakresie procesów oraz stosunków społecznych.
Diagram Ishikawy
Diagram Ishikawy stanowi obecnie bardzo powszechne narzędzie w zarządzaniu jakością oraz Lean Management. Jego istotą jest graficzna prezentacja analizy wzajemnych powiązań przyczyn wywołujących określony problem. Może być on wykorzystany na etapie definiowania problemu, ustalania przyczyn oraz weryfikacji alternatywnych rozwiązań problemu. Diagram Ishikawy często nazywany jest także schematem jodełkowym, lub też schematem rybiej ości, bowiem wyglądem swoim przypomina jej kształt.
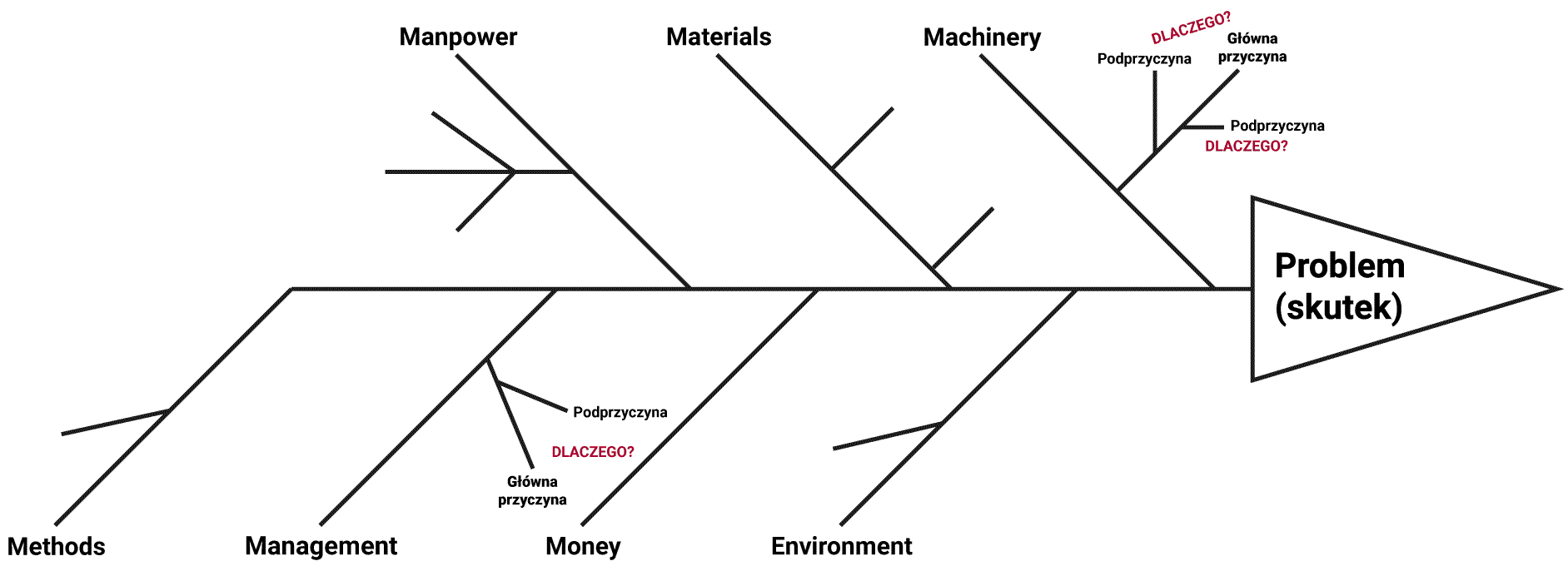
Etapy postępowania:
- Zdefiniowanie problemu – skutku
- Określenie głównych przyczyn
- Narysowanie/przygotowanie diagramu
- Umieszczenie zidentyfikowanych czynników/przyczyn na wykresie z podziałem na określone kategorie
- Rozwinięcie wskazanych przyczyn problemu
- Sprawdzenie czy nie pominięto jakiś czynników
- Ustalenie czynników, które silnie wpływają na problem
- Przekazanie uczestnikom wykresu i wyciągniętych wniosków
Diagram Ishikawy jest stosunkowo elastycznym narzędziem, można kreować własne kategorie wg potrzeby. Na przykład częstą kategorią, która pojawia się w analizach organizacji usługowych jest klient. Należy jednak mieć na uwadze, że Diagram Ishikawy z góry narzuca kategorie analizy co może w pewien sposób usztywniać pracę zespołu. Pojawia się też pokusa poszukiwania przyczyn „na siłę”, po to, aby tylko dana kategoria nie postała pusta na wykresie. Trudno też zapewnić uczestnikom anonimowość. Ocena przyczyn i wybór tych najbardziej prawdopodobnych jest wynikiem analizy jakościowej, i nie jest poparta obliczeniami.
Techniki grupowania kategorii w Diagramie Ishikawy
- Man power (pracownicy) - kwalifikacje, przyzwyczajenia, zadowolenie z pracy, staż, samopoczucie, itp.
- Method (metoda) - procedury, instrukcje, zakres obowiązków, specyfikacje, normy, prawo, reguły, know-how, technologia, itp.
- Mahinery (maszyna) – infrastruktura materialna, licencja, trwałość, nowoczesność, wydajność, precyzja, bezpieczeństwo, warunki pracy, itp.
- Material (materiał) - surowce wejściowe, półfabrykaty, elementy, substytuty, materiały biurowe itd.
- Management (zarządzanie) – struktura organizacyjna, organizacja pracy, zmianowość, warunki pracy, itp.
- Measurement (pomiary, system pomiarowy) – rozwiązania w zakresie pomiarów, oceny, urządzeń, systemów i metod pomiarowych
- Money (zasoby finansowe) – stan finansowy, koszty obsługi zadłużenia, kapitał, cena itp.
- Environment (otoczenie zewnętrzne) – czynniki środowiska naturalnego, stan dróg i połączeń,
Przykład wykorzystania diagramu Ishikawy
PROBLEM: Znaczny procent zarejestrowanych osób nie przychodzi na konferencje, nie zgłaszając równocześnie rezygnacji z uczestnictwa tym samym blokując miejsca.
Analiza problemu – zebrano dane dotyczące uczestnictwa w konferencji:
Uczestnictwo w konferencji – statystyka
Luty 2018
- ilość osób, które się zgłosiły, a nie przyszły – 14 % (48 osób)
- ilość osób zarejestrowanych (łącznie z nieobecnymi) – 368 osób
Wrzesień 2018
- ilość osób, które się zgłosiły, a nie przyszły – 17 % (74 osoby)
- ilość osób zarejestrowanych (łącznie z nieobecnymi) – 446 osób
Luty 2019
- Obecnie (styczeń 2019) overbooking 16 % i po osiągnięciu takiego stanu zamknięto zapisy;
- Średnio 1-2 % rezygnujących i zgłasza to przed wydarzeniem, reszta po prostu się nie pojawia.
Konsekwencje: rezygnacja sponsorów, ryzykowny overbooking.
Rozwiązanie problemu:
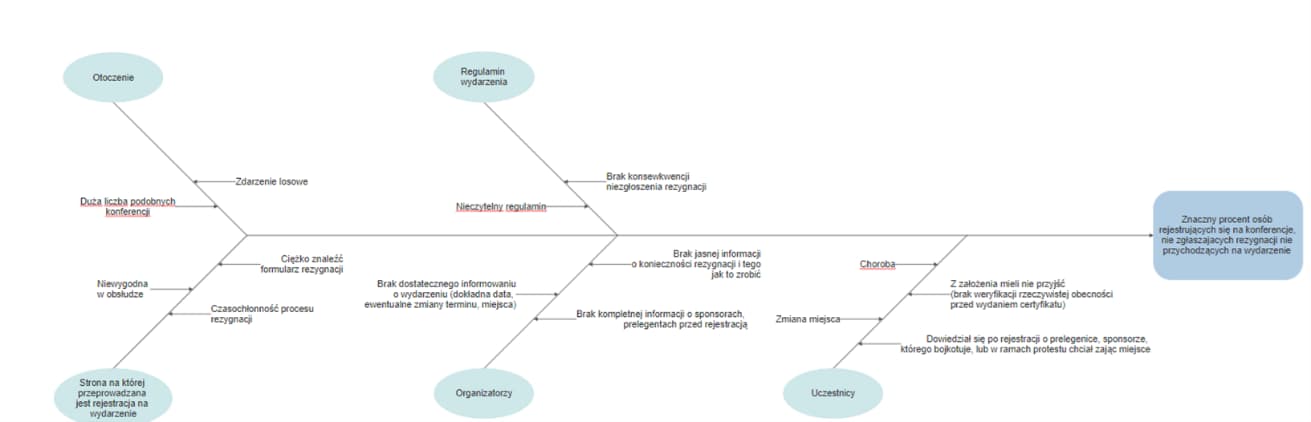
Po przeprowadzonej analizie, zespół doszedł do wniosku, że główną przyczyną problemu jest skomplikowany i niejasny dla uczestników proces rezygnacji z udziału w konferencji, brak możliwości zgłoszenia rezygnacji (często zgłoszenia na konferencje są dokonywane grupowo przez firmę), oraz brak systemu przypominania o konferencji lub potwierdzania udziału w konferencji.
Arkusz kontrolny
Arkusz kontrolny umożliwia ewidencję danych oraz rozpoznawanie prawidłowości w procesie spiętrzania się określonych zjawisk w bezpośrednim powiązaniu z częstością ich występowania[7]. Narzędzie to służy do zbierania i porządkowania danych z pomiarów i obserwacji. Może być ono wykorzystane na wszystkich etapach rozwiązywania problemu, a w szczególności do zbierania danych ilościowych opisujących kształtowanie się mierzonej wielkości (np. czas, defekty, satysfakcja klienta), analizowania zebranych danych, kontroli wyników wprowadzonych działań usprawniających. W odróżnieniu od wcześniej prezentowanych technik i narzędzi tj. 5Whys, 5W2H, diagram pokrewieństwa, diagram Ishikawy, arkusz kontrolny jest narzędziem do zbierania danych ilościowych. Arkusz kontrolny możemy stosować jako samodzielne narzędzie badawcze, lub łączyć z innymi narzędziami jakościowymi i ilościowymi. Na przykład arkusz kontrolny może być wykorzystany do zbadania częstości występowania przyczyn problemu zdefiniowanego w Diagramie Ishiskawy.
Etapy realizacji:
- Określnie celu opracowania arkusza kontrolnego
- Określenie rodzaju danych, które mają być zawarte w arkuszu
- Ustalenie czasu oraz metod zbierania danych
- Opracowanie wstępnego projektu arkusza i jego konsultacja
- Wersja ostateczna arkusza
- Zbieranie danych
- Analiza wyników badań i projektowanie działań doskonalących
Arkusz kontrolny jest prostym i mało kosztownych narzędziem zbierania i analizowania danych. Pozwala na odkrycie zjawisk w procesach, których nie jesteśmy w stanie wyczytać z prostej analizy dokumentacji, rejestrów i zestawień. Wada arkusza kontrolnego może być ograniczony zakres danych, który podlega badaniu w jednym czasie. Musi być on skrupulatnie i na bieżąco wypełniany, co wymaga dyscypliny osób odpowiedzialnych.
Przykład wykorzystania arkusza kontrolnego
PROBLEM: Pracownicy skarżą, się na przewlekłość procesu rozpatrywania wniosków, duża ich część nie jest rozpatrywana w założonym regulaminowym terminie do 40 dni.
W związku z zaistniałą sytuacją zebrano informacje nt. czasu trwania procesy rozpatrywania 77 wniosków. Dane zestawiono w postaci arkusza kontrolnego.
Wartość /cecha | Ilość |
Wnioski rozpatrzone do 10 dni | 4 |
Wnioski rozpatrzone od 11 do 20 dni | 11 |
Wnioski rozpatrzone od 21 do 30 dni | 14 |
Wnioski rozpatrzone od 31 do 40 dni | 10 |
Wnioski rozpatrzone pow. 41 dni | 35 |
Wnioski nierozpatrzone | 3 |
Suma wniosków | 77 |
Przeprowadzona analiza wskazuje, że największa ilość wniosków jest w czasie powyżej 41 dni. Zatem proces wymaga dokładnej dalszej analizy i restrukturyzacji.
Metoda Pareto
Metoda Pareto umożliwia zidentyfikowanie czynników (zdarzeń, przyczyn) mających największy wpływ na wybrane wielkości opisujące wynik procesu lub charakterystykę produktu lub problem zidentyfikowany w organizacji. Pozwala ona na hierarchizację czynników wpływających na badane zjawisko i wskazanie tych, które wpływają na to zjawisko w największym zakresie[8]. Diagram Pareto jest graficznym obrazem pokazującym zarówno względny jak i bezwzględny rozkład rodzajów błędów, problemów lub ich przyczyn. Został on rozpowszechniony przez Josepha M. Jurana który zajmował się analizą nierównomiernego rozkładu strat jakości[9]. W przypadku zastosowania Diagramu Pareto-Lorenza w praktyce zarządzania, zgodnie z regułą 80/20 należy skupić się na przeprowadzeniu działań korygujących właśnie w stosunku do tych najistotniejszych 20% przyczyn niezgodności.
Etapy realizacji:
- Określenie celu badania i zebranie danych
- Analiza danych
- Analiza wyników. Wnioski dla menedżera.
Metoda Pareto pozwala na wskazanie głównych tych przyczyn występujących problemów, co w sytuacji ograniczonych zasobów, daje możliwość określanie najbardziej optymalnych wariantów rozwiązań problemów. Pozwala na lepszą alokację zasobów w procesie doskonalenia działań i procesów. Zastosowanie tej metody wymaga zebrania danych ilościowych, co często może stanowić pewne utrudnienie, gdyż wymaga zaprojektowania dedykowanych narzędzi badawczych.
Poniżej zaprezentowano przykład wykorzystania metody Pareto do analizy przyczyn wypalenia zawodowego pracowników.
Przykład wykorzystania metody Pareto
PROBLEM: Wzrasta poziom wypalenia zawodowego pracowników w organizacji.
Opis: W ciągu ostatniego roku:
- Maleje wskaźnik jakości życia w miejscu pracy (2020 – 4,0 do 2021 – 3,8, skala 1-5)
- Wzrasta wskaźnik absencji (2020 – ilość dni nieobecności - średnio 10 na 1 pracownika, 2021 – 14 dni na 1 pracownika)
- Wzrasta wskaźnik rotacji pracowników (2020 – 1%, 2021 – 1,5 %)
Wśród pracowników przeprowadzono badanie ankietowe, w którym poproszono ich o wskazanie jednej najważniejszej ich zdaniem przyczyny wypalenia zawodowego.
W tabeli przedstawiono wyniki badania.
lp. | Przyczyna wypalenia zawodowego | liczba osób, które wybrały daną przyczynę |
1. | brak możliwości rozwoju | 5 |
2. | brak współpracy z przełożonym | 1 |
3. | montonność pracy | 1 |
4. | procedury uniemożliwiające działanie | 2 |
5. | przeciążenie pracą | 3 |
6. | trudność wprowadzania zmian usprawniających | 1 |
7. | zarobki nieadekwatne do nakładu pracy | 2 |
| Suma | 15 |
W kolejnym etapie przeprowadzono analizę danych. Przyczyny uporządkowano malejąco według ilości wskazań. Następnie obliczono udział procentowy każdej z przyczyn w sumie wskazań oraz skumulowany szereg procentowy. Na podstawie wartości skumulowanego dokonuje się podziału przyczyn na 3 grupy:
- obszar A do 80 %
- B od 80% do 95%
- C od 95%
Na końcu opracowany jest wykres Pareto.
lp. | przyczyna wypalenia zawodowego | liczba osób, które wybrały daną przyczynę | Udział procentowy przyczyny w sumie wskazań | Wartość skumulowana w % | Określenie części ABC |
1. | brak możliwości rozwoju | 5 | 33% | 33% | A |
2. | przeciążenie pracą | 3 | 20% | 53% | A |
3. | procedury uniemożliwiające działanie | 2 | 13% | 67% | A |
4. | zarobki nieadekwatne do nakładu pracy | 2 | 13% | 80% | A |
7. | brak współpracy z przełożonym | 1 | 7% | 87% | B |
14. | trudność wprowadzania zmian usprawniających | 1 | 7% | 93% | B |
15. | monotonność pracy | 1 | 7% | 100% | C |
SUMA | 15 | 100% | – |
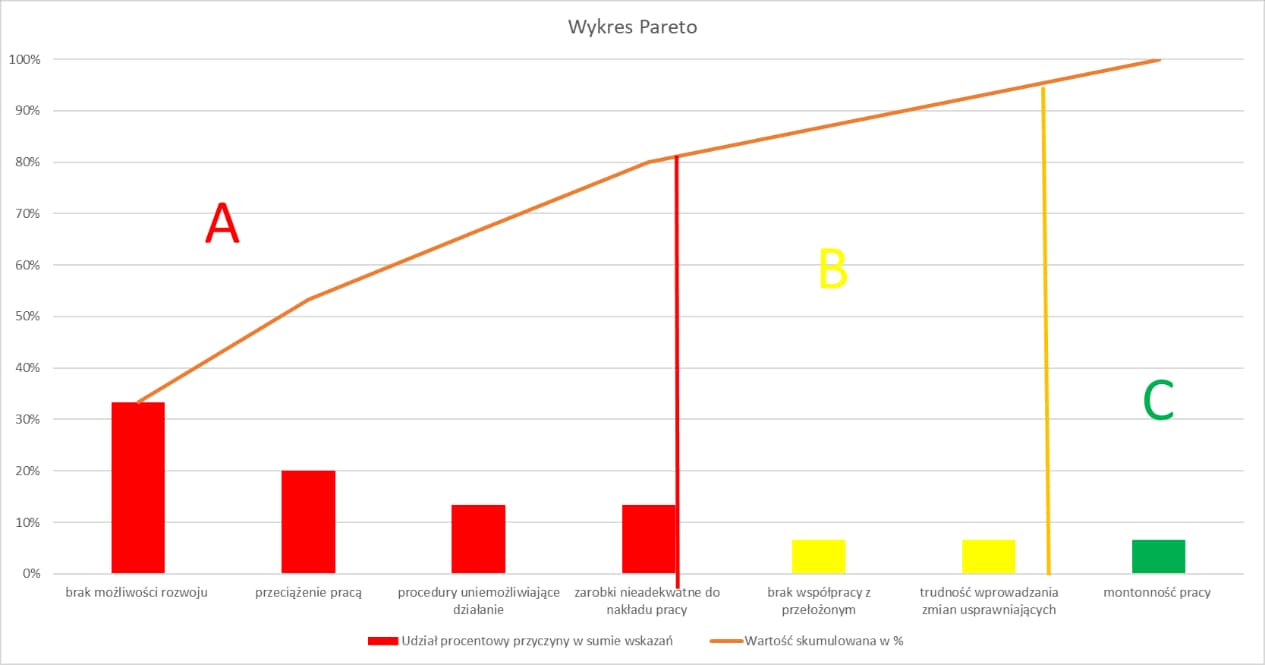
Wyniki analizy pokazują, że do najważniejszych przyczyn wypalenia zawodowego (obszar A) można zaliczyć:
- brak możliwości rozwoju
- przeciążenie pracą
- procedury uniemożliwiające działanie
- zarobki nieadekwatne do nakładu pracy
Są to przyczyny, które zostały wskazane przez 80% badanych pracowników. Od nich kierownictwo powinno rozpocząć program zmiany ukierunkowany na zmniejszenie zjawiska wypalenia zawodowego wśród pracowników. Zaproponować działania korygujące, korekcyjne oraz profilaktyczne.
Techniki mapowania
SIPOC
Technika SIPOC (Supliers, Inputs, Process, Outputs, Customer) oparta jest na założeniu, że wszystko, co jest treścią procesu zorientowane jest na klienta, wynika z jego potrzeb oraz oczekiwań. Zatem projektowanie procesu odbywa się w konwencji łańcucha tworzenia wartości dla klienta[10]. SIPOC w procesie rozwiązywania problemów jest wykorzystywany do definiowania problemów, poszukiwania ich przyczyn, projektowania i wyboru wariantów rozwiązania.
Ideę SIPOC przedstawia rysunek.
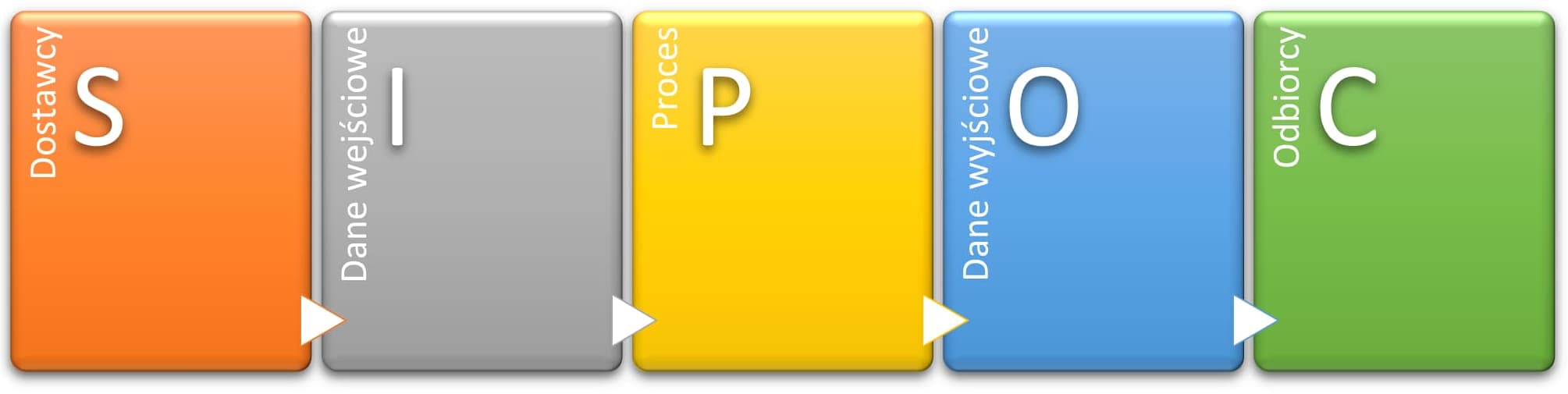
SIPOC może być z powodzeniem wykorzystany do mapowania już istniejących procesów, ich przeprojektowywania lub projektowania nowych procesów. Pozwala on na zebranie i uporządkowanie informacji o procesie oraz uzupełnienie brakujących elementów ważnych z punktu zarządzania procesem (np. wskaźników procesowych). SIPOC występuje w różnych formach graficznych – diagramów, tabel, grafów. Przykładową tabelę do analizy procesu z wykorzystaniem SIPOC prezentuje rysunek.
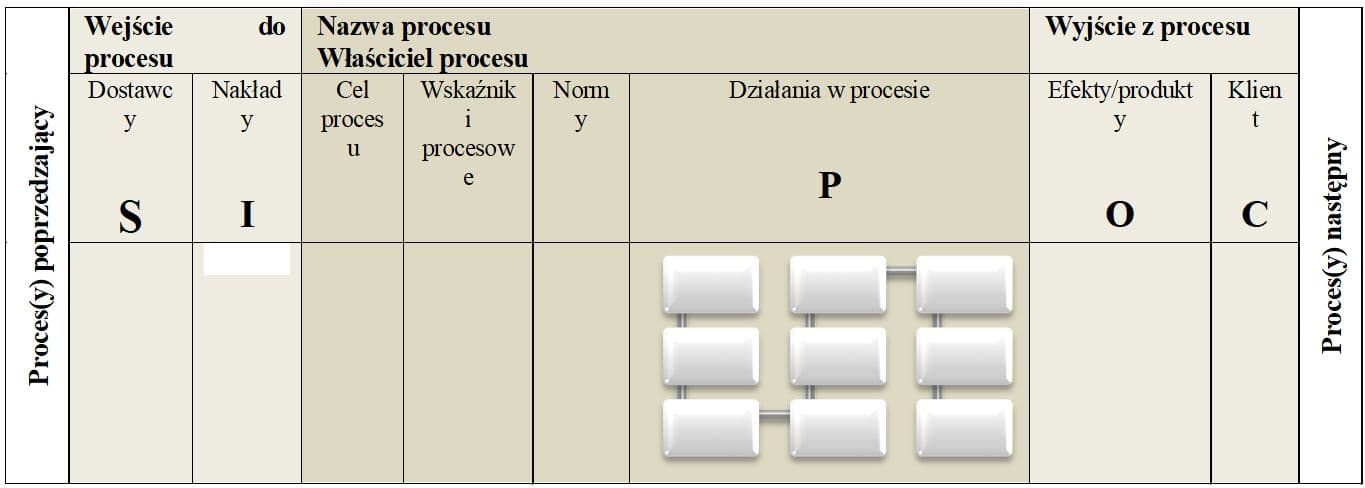
Etapy realizacji:
- Identyfikacja właściciela procesu
- Identyfikacja klienta procesu i jego wymagań
- Identyfikacja produktu procesu
- Identyfikacja celu, wskaźników procesowych i przebiegu procesu
- Identyfikacja nakładów
- Identyfikacja dostawców
Celem SIPOC jest danie ogólnego obrazu procesu, zatem informacje zamieszone w diagramie/tabeli mają charakter ogólny i generalny. Analizy szczegółowe są przeprowadzane z wykorzystaniem innych narzędzi takich jak schemat blokowy (flowchart) czy mapowanie strumienia wartości.
SIPOC jest stosunkowo intuicyjnym i prostym narzędziem mapowania procesu, które może być wykorzystane przez pracowników nie posiadając specjalistycznej wiedzy w zakresu zarządzania procesami. SIPOC może stanowić etap przygotowujący procesy do automatyzacji. Należy jednak zwrócić uwagę na poziom generalizacji i szczegółowości opisu procesu, tak, aby nie był on ani zbyt ogólny, ani zbyt szczegółowy.
WEJŚCIE | PROCES Usługa hotelowa Właściciel procesu: kierownik hotelu | WYJŚCIE | |||||
Dostawca | Dane wejściowe | Realizowane działania | Cel | Wskaźniki skuteczności i efektywności | Norma wskaźnika | Dane wyjściowe (wynik procesu) | Klient/ odbiorca |
Dostawcy wyposażenia hotelowego. Dostawca urządzeń i oprogramowania informatycznego. Dostawca materiałów (np. środków czystości, środków higienicznych). Inne działy organizacji (restauracja, centrum sportu i rekreacji, dział finasowo-księgowy) | Zlecenie klienta. Lista żywieniowa. Rozporządzenie Ministra Gospodarki kategoryzacji sprawie obiektów hotelarskich. Instrukcja ustalania i stosowania cen za usługi Regulamin Organizacyjny Cennik usług Ośrodka. Zbiór obowiązków pracowników działu hotelowego. Instrukcja komputerowego systemu obsługi hotelu „GOŚĆ”. | przyjęcie zlecenia | Dostarczenie klientowi pełnej satysfakcji z pobytu w hotelu | -poziom zadowolenia klienta (skala oceny 1-5) | -wartość wskaźnika pomiędzy 4,5 – 5,0 | Skutecznie wykonana usługa hotelowa | Klient indywidulany, klient grupowy |
-ilość usług dodatkowych, z których skorzystał klient | – min. 2 | ||||||
-poziom bezpieczeństwa klienta (ilość przypadków kradzieży itp.) | -0 przypadków | ||||||
-poziom czystości w pokojach | -0 przypadków braku czystości -czas przygotowania pokoju |
Tabela 6.2. Projektowanie procesu Usługa hotelowa. Źródło: opracowanie własne
Schemat blokowy (flowchart)
Schemat blokowy (flowchart) jest graficzną prezentacją przebiegu procesu. Pozwala na zrozumienie, analizę, korektę, modyfikacje i doskonalenie procesu. Schemat blokowy w procesie rozwiązywania problemów jest wykorzystywany do definiowania problemów, poszukiwania ich przyczyn, projektowania i wyboru wariantów rozwiązania. Schemat blokowy jest rysunkiem, na którym poprzez zastosowanie odpowiednych symboli oznacza się elementy procesu. Poniższy rysunek prezentuje przykładowy schemat blokowy.
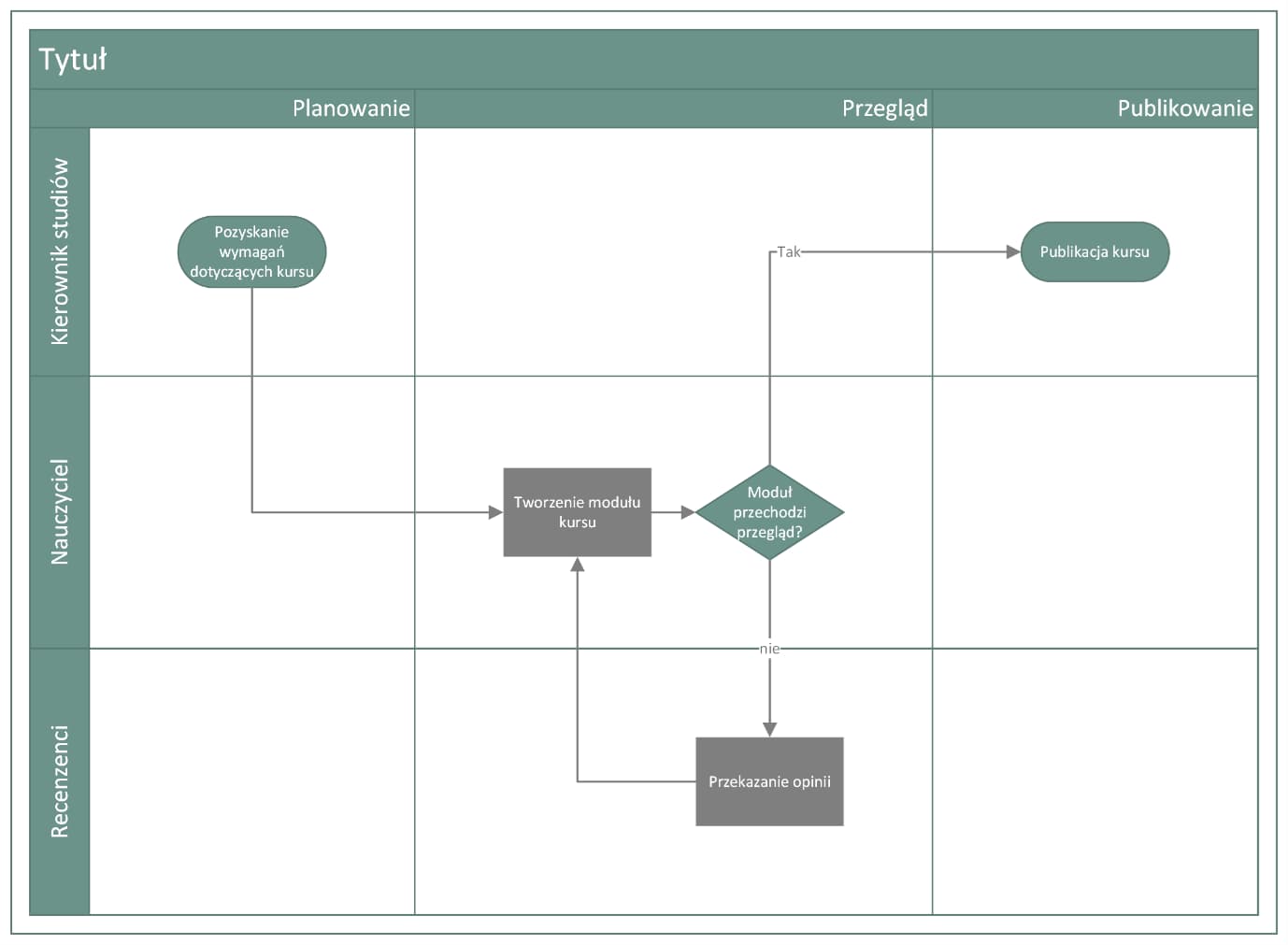
Typowe oznaczenia stosowane w schematach blokowych to:
Terminator – początek, koniec procesu
Proces – etap procesu
Decyzja – wybór ścieżki realizacji procesu w zależności od decyzji (tak/nie)
Strzałka oznacza kierunek przebiegu procesu
Na początkowym etapie pracy nad schematami blokowymi proste oznaczenia są najbardziej przydatne. W momencie, kiedy proces jest przygotowany do automatyzacji czy informatyzacji stosuje się wystandaryzowane notacje np. Business Process Model and Notation, BPMN (Notacja i Model Procesu biznesowego). Jest to graficzna notacja służąca do opisywania procesów biznesowych. Dodatkowo proces można opisać poprzez fazy jego realizacji oraz odpowiedzialnych za poszczególne działania (swimlanes flowchart).
Poniżej scharakteryzowano etapy przygotowania schematu blokowego. Należy mieć na uwadze, że mogą one mieć inny przebieg lub zakres podejmowanych czynności w zależności od celu opracowania schematu.
Etapy realizacji:
- Gromadzenie i analiza informacji i danych na temat procesu
- Identyfikacja początku i końca procesu
- Identyfikacja i mapowanie przebiegu procesu - model as is
- Konstruowanie, przegląd i doskonalenie wstępnego projektu schematu blokowego – model to be
- Przygotowanie programu wdrażania nowego/udoskonalonego procesu
Schemat blokowy porządkuje, ujednolica i standaryzuje realizację procesu w organizacji. Największym zagrożeniem może być nadmierna szczegółowość opisu.
Mapowanie strumienia wartości VSM
Podstawową techniką oraz narzędziem mapowania procesów stosowanym w Lean Management jest Mapowanie Strumienia Wartości (Value Stream Mapping VSM). VSM w procesie rozwiązywania problemów jest wykorzystywane do definiowania problemów, poszukiwania ich przyczyn, projektowania i wyboru wariantów rozwiązania. Kluczowymi pojęciami w VSM są: wartość oraz marnotrawstwo. Celem VSM jest identyfikacja, analiza i ocena wszystkich czynności i działań podejmowanych w procesie z punktu widzenia tworzenia wartości dla klienta procesu. Wartość dodaną tworzą te działania:
- za które klient chce zapłacić,
- które zmieniają produkt (zmieniają jego charakterystyki lub wyposażają w te, które docelowo mają spełniać wymagania i oczekiwania klienta procesu),
- jest wykonane dobrze za pierwszym razem, bez błędów i powtórnej pracy.
Wartość jest tworzona w strumieniu wartości (value stream), który obejmuje wszystkie działania (zarówno dodające jak i nie dodające wartości) wymagane w procesie realizacji usługi od projektowania do dostarczenia klientowi (tzw. przepływy)[11]. Istotą mapowania jest wskazanie tych działań, które tworzą wartość i eliminacji lub minimalizacji tych które jej nie tworzą (są źródłem marnotrawstwa tzn. zużywają zasoby i czas, a nie tworzą wartości dla klienta.). Mapowanie strumienia wartości pozwala na realizację wszystkich zasad Lean (value, value stream, flow, pull, continuous improvement).
Do mapowania procesu wykorzystuje się mapę strumienia wartości – jest to rysunek prezentujący charakterystykę przebiegu danego procesu, ze wskazaniem przepływu wartości. Na mapie strumienia wartości przedstawia się informacje o[12]: zapotrzebowaniu klientów i ich zmienności, wymaganiach klienta, sposobie komunikacji z klientem, formie i czasie trwania przepływu informacji wewnątrz organizacji, zasadach komunikacji z dostawcami i ich charakterystyki, zapasach i szczegółach procesu realizacji usług, problemach utrudniających lub wydłużających czas realizacji zlecenia, czasie jaki potrzebny jest na przemianę gotówki zainwestowanej w materiały na gotówkę, która wpływa od klienta za dostarczone mu usługi (tzw. Lead Time – L/T).
Ideę VSM przedstawia rysunek.
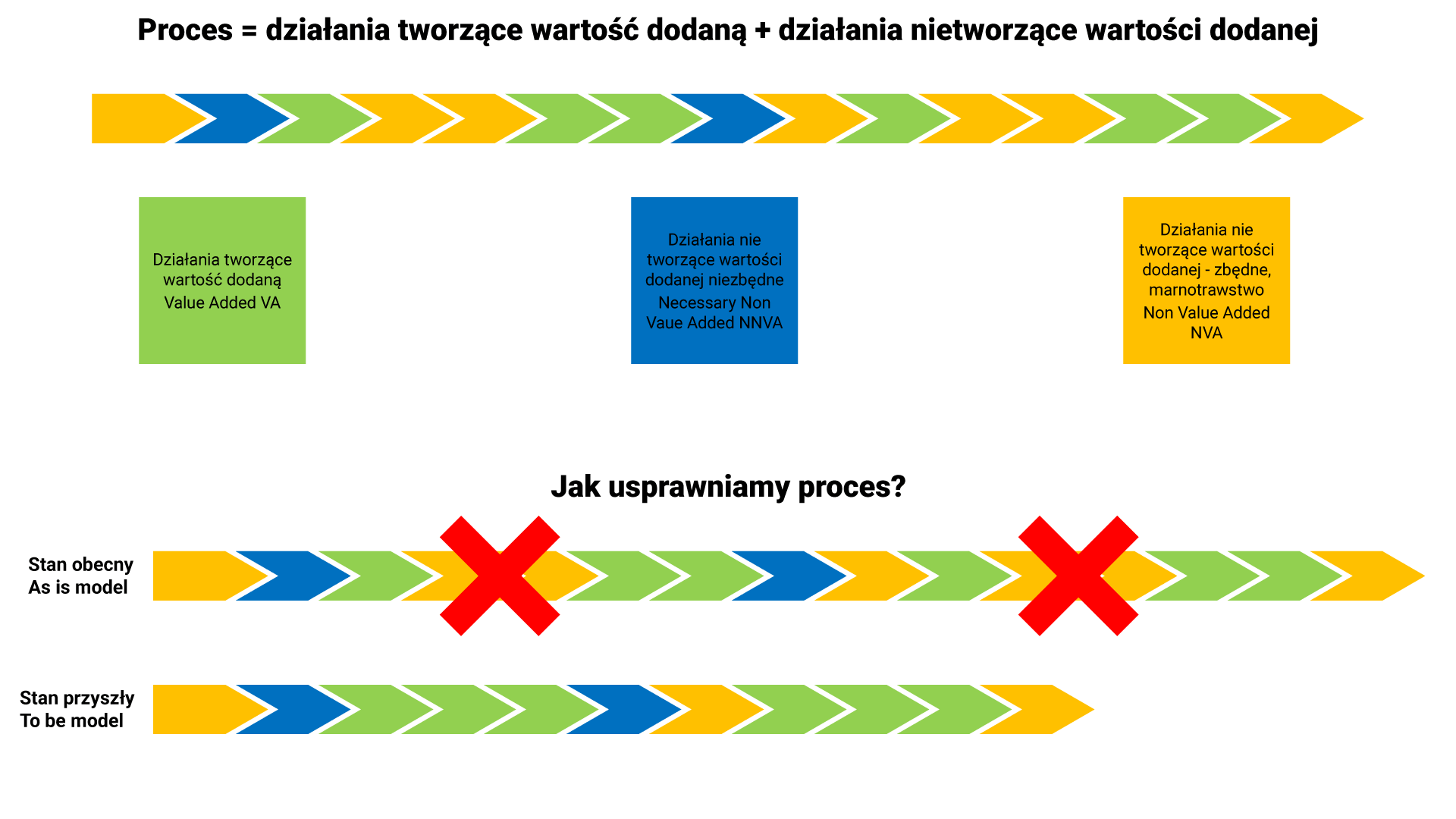
Najważniejszym miernikiem strumienia wartości jest czas definiowany poprzez:
- L/T Lead Time – całkowity, nominalny czas trwania procesu, wynikający z uregulowań zewnętrznych lub wewnętrznych
- P/T Processing Time – faktyczny czas realizacji procesu,
- VAT value added time – czas tworzenia wartości dodanej, sumaryczny czas wszystkich czynności w procesie, które zdefiniowano jako tworzące wartość dla klienta.
- NVAT/NNVAT – non value added time/ necessary non value added time – czas działań, które nie tworzą wartości dodanej (działań tworzące marnotrawstwo).
- T/T czas taktu klienta – czas pracy dostępny w trakcie jednej zmiany/ilość zamówień klienta (obliczając czas pracy należy odjąć czas przerw w pracy oraz czas planowanych przestojów i konserwacji np. systemów IT).
- Wydajność procesu – ilość produktów/czas pracy dostępny w trakcie jednej zmiany.
- Wskaźnik dotrzymania wymagań dotyczących czasu trwania procesu (jeśli takie zostały określone, można je wyrazić procentowo np. ilość procesów zrealizowanych w wymaganym czasie/wolumenu procesów w danym okresie x 100%).
Można również wykorzystać dodatkowe mierniki adekwatne do specyfiki procesu.
Etapy realizacji:
- Wybór procesu, zidentyfikowanie klienta, zdefiniowanie oczekiwań klienta oraz tworzonej dla niego wartość.
- Przeprowadzenie diagnozy czynności i działań składających się na strumień wartości, określenie ich kolejności oraz ich charakteru. Wstępna identyfikacja źródeł marnotrawstwa i działań usprawniających.
- Pomiar czasu działań, czasu oczekiwania oraz innych mierników.
- Zbadanie zmienności procesu, określenie średniego miesięcznego zapotrzebowania oraz taktu klienta.
- Określić miejsca tworzenia się w procesie zapasów, zaznaczyć linię czasu, obliczyć L/T, P/P, T/T i wydajność procesu.
- Określenie czynności, które dodają wartości i tych, które są źródłem marnotrawstwa, VAT, NVAT, NNVAT.
- Zaznaczenie przepływu informacji ma mapie.
- Analiza mapy strumienia wartości i opracowanie nowej modelu to be procesu. Przygotowanie programu zarządzania zmianą.
Mapa strumienia wartości może być przygotowana w różnych wersjach, mniej lub bardziej rozbudowanych. Typowe symbole umieszczane na mapie wartości oraz mapę strumienia wartości umieszczono poniżej na rysunkach.
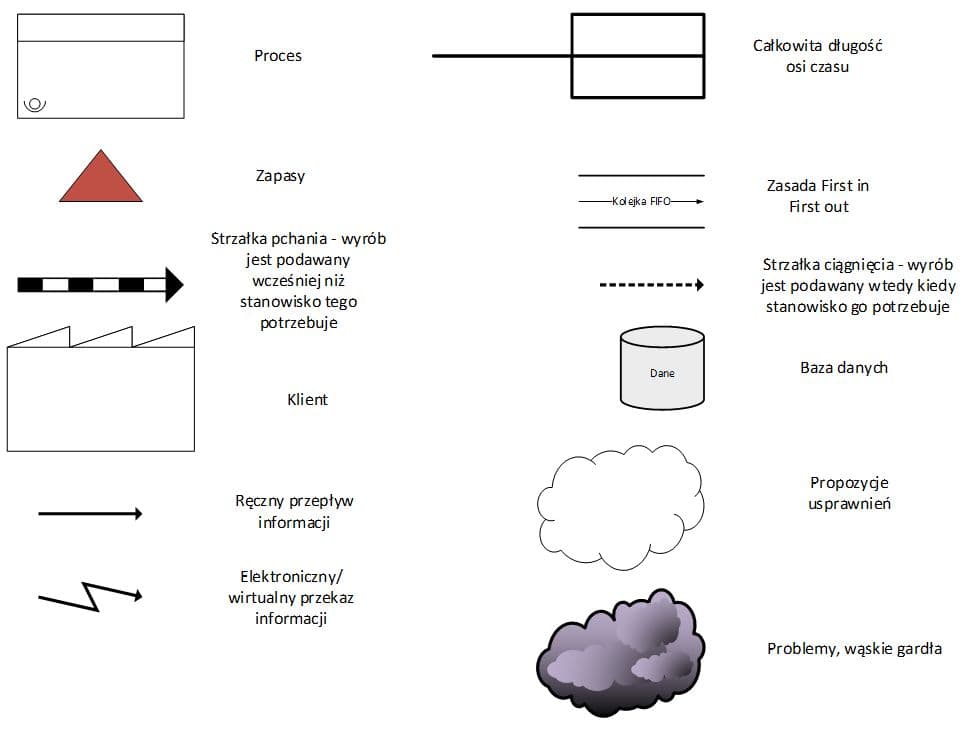
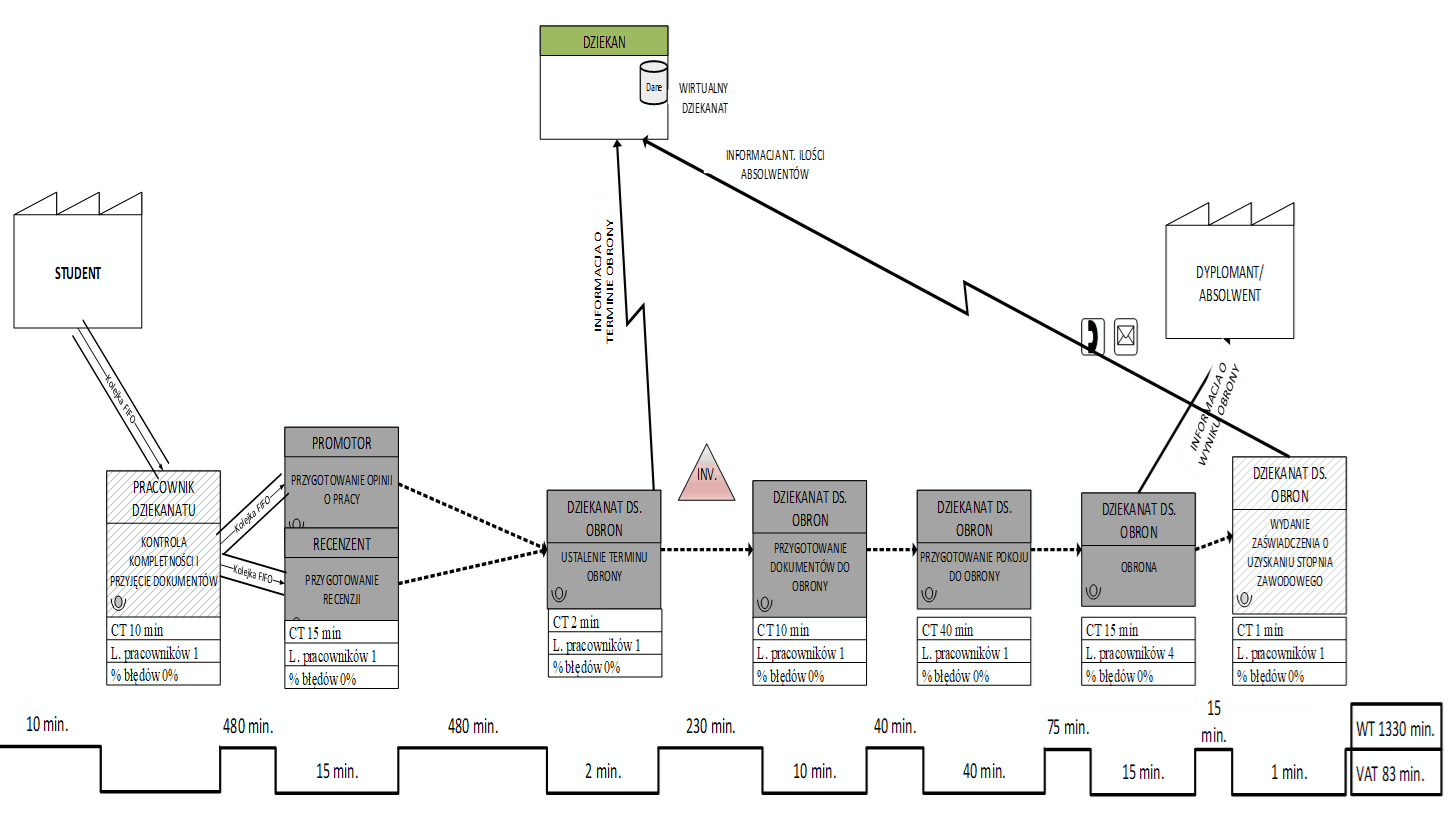
Mapowanie strumienia wartości ma swoje genezę w przedsiębiorstwach produkcyjnych oraz biznesie. Coraz częściej jest ona wykorzystywana w organizacjach publicznych i pozarządowych oraz do mapowania procesów administracyjnych w przedsiębiorstwach. Można wtedy zastosować jej uproszoną wersję. W najprostszej wersji do wykonania mapy strumienia wartości można wykorzystać arkusz papieru i kolorowe karteczki post-it-notes. Poszczególne kolory karteczek mogą oznaczać:
Kolor zielony – pomysły usprawnień
Kolor żółty – działania w procesie
Kolor różowy – źródła marnotrawstwa
Kolor pomarańczowy – dodatkowe informacje.
Oznaczenia kolorów mają charakter umowy. Poniższe zdjęcie pokazuje przykład takiej mapy.
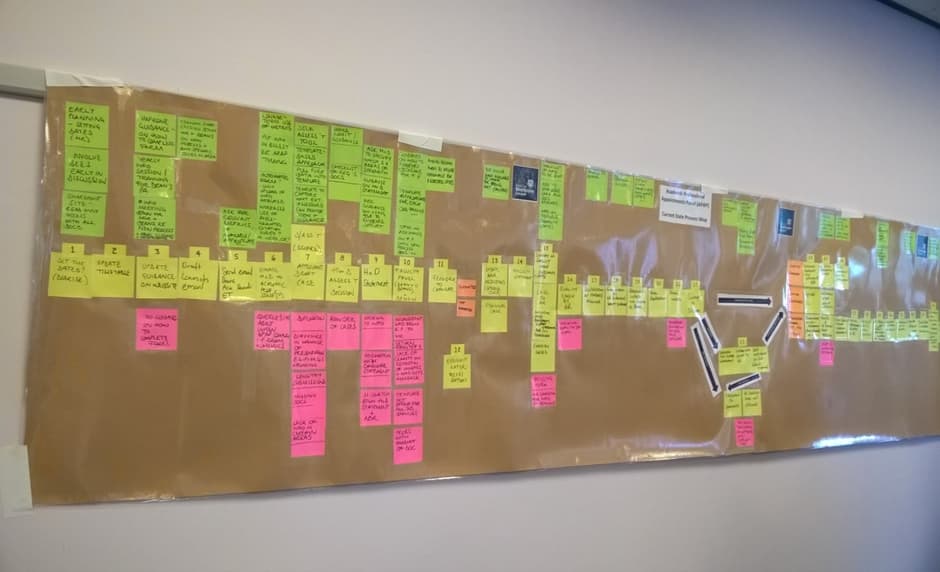
Mapowanie strumienia wartości pozwala na pokazanie tego co faktycznie organizacja robi, jakie są źródła marnotrawstwa w procesach, a co stanowi wartość. Wykorzystanie mapy strumienia wartości przynosi liczne korzyści takie jak: szybkie poznanie procesu i zidentyfikowanie problemów, lepsza alokacja pracowników w procesach, lepsze wykorzystanie zasobów, zrównoważenie pracy. Dodatkowo mapa procesów pokazuje perspektywę doskonalenia oraz motywuje do usprawniania.
Kompleksowe podejścia do rozwiązywania problemów
Arkusz A3
Arkusz A3 jest raport jednostronicowy, który pozwala na wizualizacje wszystkich działań, które są podejmowane w procesie nieustannego doskonalenie procesów i działań w cyklu PDCA. Celem arkusza jest prezentacja i opis problemu oraz sposób jego rozwiązania wraz z weryfikacja i doskonaleniem. Zazwyczaj składa się on z następujących części: opis problemu, źródło problemu, możliwe środki zaradcze, podjęte kroki zaradcze, rezultaty i dalsze wymagane działania. Arkusz pozwala na skuteczną komunikację między członkami zespołu oraz innymi interesariuszami w procesie rozwiązywania problemu, opis stanu zaawansowania działań w kolejnych etapach, planowanie kolejnych działań profilaktycznych i zapobiegawczych oraz podejmowanie racjonalnych decyzji opartych na danych i faktach. Struktura arkusza oparta jest na modelu PDCA. Przykładowy Arkusz A3 przedstawiono poniżej.
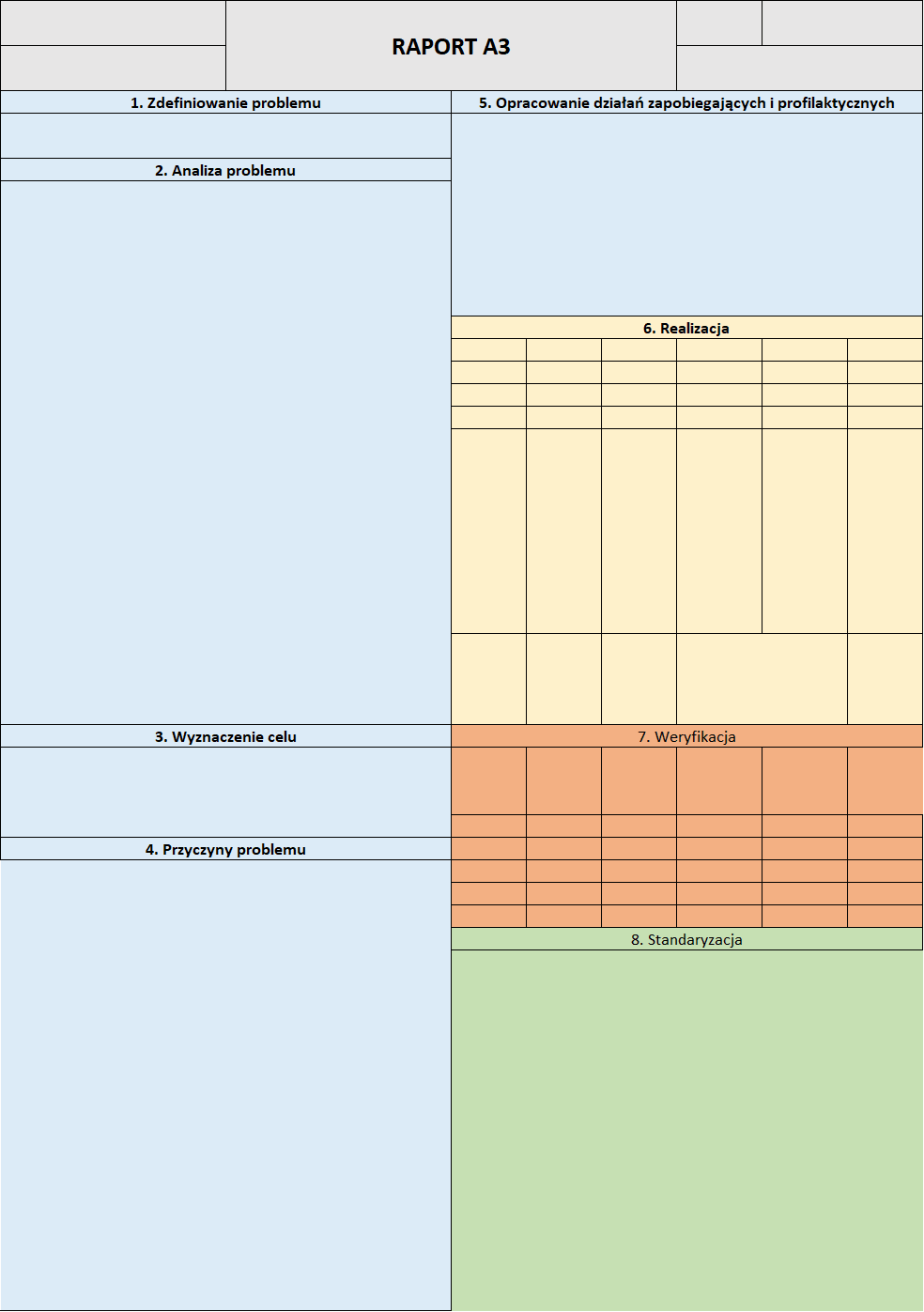
- konkretność, oparcie na danych i faktach,
- wizualizacja,
- konieczność przeanalizowanie całego cyklu PDCA,
- możliwość monitorowania wprowadzonych zmian,
- przechowywanie wiedzy i dobrych praktyk,
DMAIC
DMAIC jest centralna osią, wokół które skupiają się działania w zakresie rozwiązywania problemów z wykorzystaniem metodyki Six Sigma. Celem Six Sigma jest doskonalenie procesów poprzez redukcję ich zmienności poprzez wykorzystanie metod statystycznych opartych na pomiarze odchylenia standardowego (kluczowym pojęciem jest poziom Six Sigma)[14].
Kluczowym pojęciem w tej koncepcji jest pojęcie Poziomu Sigma. Poziom Sigma jest miarą poziomu jakości, oznacza, ile razy odchylenie standardowe (oznaczone przez sigma) danej cechy mieści się w połowie pola tolerancji[15]. Poziom Six Sigma oznacza, iż występuje mniej niż 3.4 defektów na milion wystąpień danej cechy lub wskaźnik sukcesu wynosi 99.9997%. Zatem zasadniczą korzyścią płynąca z zastosowania Six Sigma jest jasno określony poziom jakości i przedziały tolerancji dla badanych parametrów procesu[16] co daje możliwość jego nadzorowania, znajdowania i eliminowania przyczyn defektów i błędów[17].
Z czasem Six Sigma ze statystycznej techniki pomiaru stała się filozofią zarządzania opartą na odpowiedniej kulturze organizacyjnej oraz zaangażowaniu kierownictwa. W szerokim ujęciu Six Sigma to[18]:
- System pomiaru (podstawowymi wskaźnikami dla procesu usługowego mogą być:
- DPMO (defects per milion oppotunities) – wskaźnik defektów na milion wystąpień = 3,4,
- Cp[19] wskaźnik zdolności procesu, który pokazuje związek pomiędzy założoną w procesie tolerancją określoną przez dolną (LSL) i górną granicą specyfikacji (USL) a całkowitą zmiennością procesu (6s)),
- DPO (defect per oppotunities) – prawdopodobieństwo defektu procesu usługowego – relacja liczby defektów do całkowitej liczby możliwości.
- Proces ciągłej poprawy (zgodnie z modelem DMAIC: Define, Measure, Analyze, Improve, Control).
- Zmiana kulturowa w organizacji (świadomość, ze wszystko można zmierzyć, nacisk na podejście, iż najpierw mierzymy, potem rozmawiamy i działamy).
Sercem metodyki Six Sigma jest model DMAIC (rysunek).
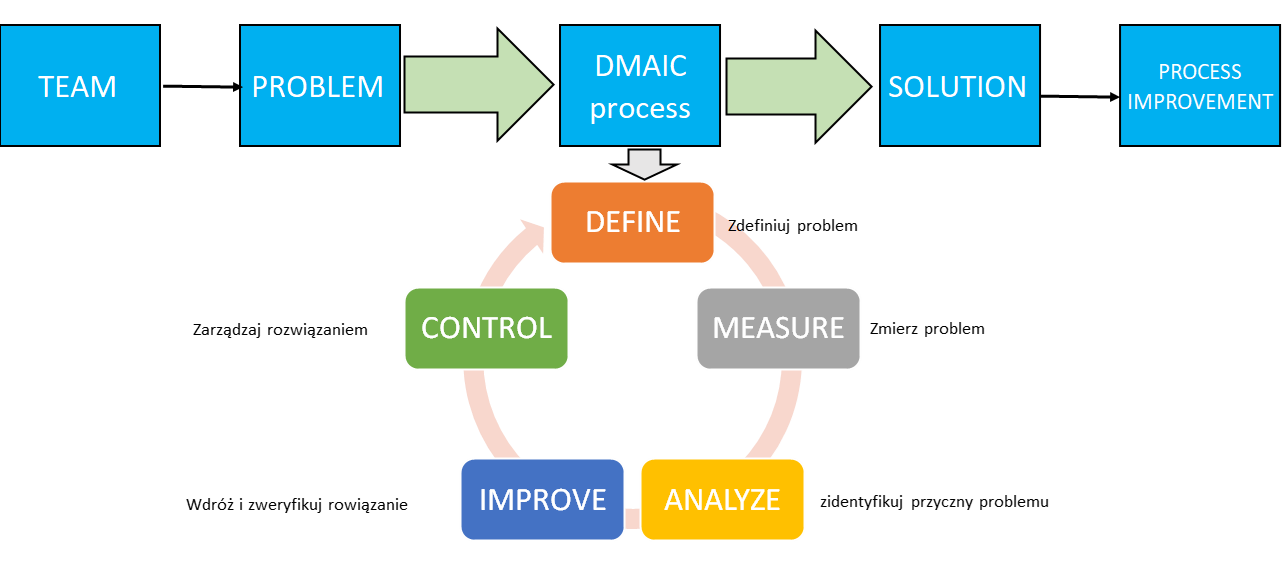
Model ma charakter uniwersalny. Oparty na cyklu PDCA pokazuje jak w usystematyzowany sposób przejść od identyfikacji i zdefiniowania problemu w organizacji do jego rozwiązania i kontroli skuteczności i efektywności zastosowanych rozwiązań.
W fazie DEFINE następuje identyfikacja problemu, jego opis, powiązanie w priorytetami organizacji, określenie zakresu problemu oraz zespołu, który będzie zaangażowany w jego rozwiązanie, określa się osoby odpowiedzialne oraz przyporządkowuje się odpowiednie zasoby do realizacji projektu. W fazie tej definiuje się też proces, w którym występuje problem (jego klientów – voice of customer oraz przebieg – wykorzystuje się często diagram SIPOC), oraz wskaźniki krytyczne dla jakości procesu (critical to quality). Można tutaj też wykorzystać tzw. siedem tradycyjnych i 7 nowych narzędzi jakości.
Faza MEASURE obejmuje działania związane z identyfikacją, pomiarem i opisem analizowanego procesu, określa się skalę problemów oraz jakie są ich dokładne źródła. W tym celu można wykorzystać narzędzia statystyczne analizy zmienności procesu, analizy ryzyk np. FMEA.
W fazie ANALYZE dokonuje się wszechstronnych analiz zebranych danych z wykorzystaniem różnych narzędzi statystycznych (analiza źródeł zmienności, analiza zdolności, analiza stabilności, analiza systemów pomiarowych, analiza zależności – korelacji i in.) i innych tj. diagram Ishikawy, metoda Pareto, arkusz kontrolny.
Faza IMPROVE obejmuje generowanie rozwiązań problemu, ocenę najlepszych alternatyw, wybór najlepszego rozwiązania problemu, przygotowanie planu wdrożenia.
Ostania faza CONTROL związana jest z przygotowaniem planu kontroli wdrożonego rozwiązania. Obejmuje ona działania w zakresie ustalenia punktów kontrolnych, zasad i planu monitorowania, standaryzacji, przeglądu wyników z kontroli i monitorowania, zakresu wprowadzania niezbędnych zmian. Zaproponowane rozwiązanie może zostać przez wdrożeniem poddany testowaniu[20] [21].
W każdej z faz DMAIC wykorzystuje się wiele metodyk i narzędzi pochodzących z zarządzania jakością, Lean management, statystycznej kontroli procesów, zarządzania zmianą czy zarządzania projektami.
Podsumowanie
Umiejętność wykorzystania metod i narzędzi Lean Management do rozwiązywania problemów staje się integralną częścią kompetencji każdego współczesnego menedżera i pracownika. Spłaszczanie struktur organizacyjnych, tworzenie samodzielnych stanowisk i zespołów, nacisk na szybkość i trafność podejmowanych decyzji w zakresie zmian powodują, że coraz więcej działań musi być podejmowanych w miejscu powstawania problemów przez pracowników bezpośrednio zaangażowanych w realizację procesów. Era podejmowania decyzji „zza biurka”, przeciągających się działań konsultacyjnych, opiniodawczych oraz długich i przewlekłych procesów decyzyjnych powoli mija. Szybkość, zwinność i elastyczność organizacji może być osiągnięta tylko przez odpowiednie reagowanie. Niezbędne jest tutaj dobre rozpoznanie kontekstu problemu i jego przyczyn oraz zaprojektowanie rozwiązań „szytych na miarę”. Instrumentarium Lean Management przedstawione w rozdziale z pewnością nie wyczerpuje tematu, daje jednak solidny fundament do pogłębiania studiów teoretycznych oraz doświadczenia praktycznego w obszarze Problem Solving.
Przypisy:
[1] PN-EN ISO 9000:2015, Systemy zarządzania jakością — Podstawy i terminologia, PKN
[2] PN-EN ISO 9000:2015,
[3] PN-EN ISO 9000:2015,
[4] Hamrol, A. (2007). Zarządzanie jakością z przykładami. Warszawa: PWN.
[5] Hamrol, A. (2007). Zarządzanie jakością z przykładami. Wydawnictwo naukowe PWN. Warszawa.
[6] Inne przykłady grupowania przyczyn to: Dla marketingu 8 P: Produkt/Product, Cena /Price, Dystrybucja /Place, Promocja /Promotion, Działalność/ Performance, Aspekty fizyczne/Physical evidence, Ludzie/People, Proces /Process; Dla usług: 4S, Dostawcy /Suppliers, Otoczenie / Surroundings, Proces/Process, Umiejętności /Skills.
[7] Hamrol, A. (2007). Zarządzanie jakością z przykładami. Warszawa: PWN.
[8] Por. Hamrol, A. (2007). Zarządzanie jakością z przykładami. Warszawa: PWN, s. 305.
[9] Łuczak, J., & Matuszak-Flejszman, A. (2007). Metody i techniki zarządzania jakością. Quality Progress, Poznań, s. 299; R. Wolniak, B. Skotnicka, Metody i narzędzia zarządzania jakością. Teoria
i praktyka, Wydawnictwo Naukowe Politechniki Śląskiej, Gliwice 2008.
[10] Grajewski, P. (2007). Organizacja procesowa. Projektowanie i konfiguracja. Warszawa: PWE, s. 123.
[11] Rother, M. and J. Shooka. (1999). Learning to see. Lean Enterprise Institiute Inc., Brookline, MA
[12] Czerska, J. (2009). Doskonalenie strumienia wartości. Difin.
[13] Liker, J. K., & Convis, G. L. (2012). Toyota way to lean leadership: Achieving and sustaining excellence through leadership development. McGraw-Hill Education.
[14] Hamrol A., Zarządzanie jakością z przykładami, PWN, Warszawa 2007; 1. Antony, J. 2004. Some pros and cons of six sigma: an academic perspective. The TQM Magazine. Vol. 16, No. 4:303-306.
[15] Hamrol A., Zarządzanie jakością z przykładami, PWN, Warszawa 2007
[16] Snee, R.D., Lean Six Sigma – getting better all the time, International Journal of Lean Six Sigma Vol. 1 No. 1, 2010, p. 14.
[17] Bandyopadhyay J.K., Lichtman R., Six Sigma Approach to Quality and Productivity Improvement in an Institution for Higher Education in the United States International Journal of Management Vol 24 No. 4 December 2007, p. 805; Snee, R.D., op. cit., p. 14.
[18] Majorana F., Morelli A., Lean Banking, Wydawnictwo M. Kraków 2012, s. 49.
[19] Czym wskaźnik Cp ma wyższą wartość, tym proces jest bardziej zdolny.
[20] Lean Six Sigm: International Standards and Global Guidelines Autorzy Terra Vanzant-Stern
[21] Process Improvement Using Six Sigma: A DMAIC Guide Autorzy Rama Shankar
Oceń ten artykuł:
Średnia ocen artykułu: / 5. Liczba ocen:
Brak ocen tego artykułu! Bądź pierwszym oceniającym.
Jedna odpowiedź
Parę lat siedzę w temacie, nie spotkałem jeszcze podobnego kompleksowego zestawienia, dziękuję.